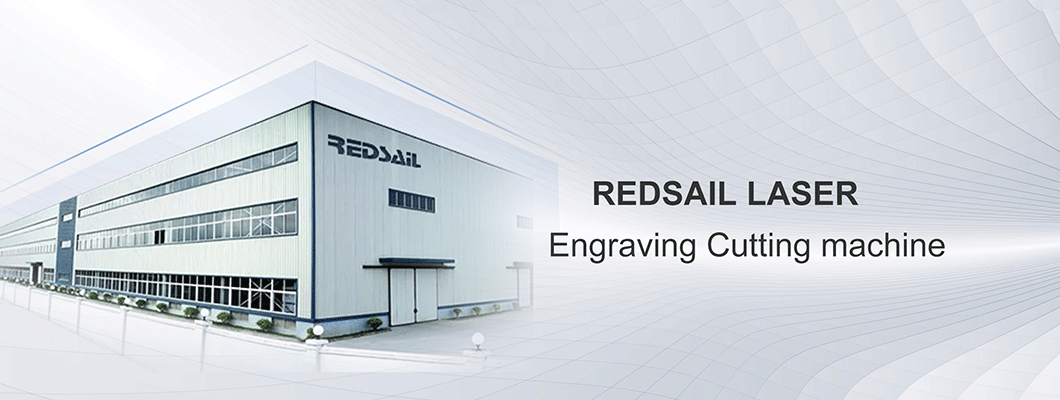
Compared with other processes, laser has the advantages of concentrated energy, strong penetration ability and high processing efficiency, but it has high requirements for the previous process. The weight of laser welding on flanging size can be reduced by 8% in the application of doors. The optimization of product structure design by laser welding can greatly reduce the processing and manufacturing links and reduce redundant design. At present, laser technology mainly involves laser welding of automobile body, cutting of hot formed sheet, laser welding of aluminum alloy, laser welding of plastics, etc.
Figure 1 Design thought process of body lightweight
Laser welding of automobile plate has the advantages of high energy, high speed, small heat affected zone and high weld quality. It has high welding accuracy, small deformation of parts, and can significantly improve the strength and stiffness of the body. It has been widely used in the manufacture of body in white.
For example, more than 1600 laser welds were used for Audi, Sagitar and Maiteng models produced by FAW Volkswagen, with a total weld length of nearly 70m. 21 laser welding machines were used for Sagitar white body, with a weld length of 9m. The strength of the whole vehicle was increased by 30%.
1. Hot forming technology and laser cutting
With the development of automobile lightweight, hot forming technology is more and more widely used in automobile industry.
Table 1 Comparison of mechanical properties between ordinary hot formed B-pillar and cold formed B-pillar
As shown in Table 1, the hot forming process combines the forming and heat treatment of steel plates, first austenitizing and then martensitizing. The strength and hardness of formed and quenched parts have been greatly improved, with the yield strength reaching more than 950MPa, and the tensile strength reaching 1500MPa, which is 2-3 times of that before heating.
The hardness can reach 420HV, which is at least twice of that before heating, but its elongation decreases significantly. Because the strength and hardness of hot formed sheet are extremely high, up to 1500 MPa, ordinary stamping equipment is difficult to process, or seriously affects the service life of equipment, and also affects the output efficiency of parts.
If ordinary thermal cutting or wire cutting is adopted, either the heat affected zone is relatively large, the cutting quality cannot meet the requirements, or it is not suitable for processing complex paths and the efficiency is low.
The laser cutting is a kind of high-energy beam processing, and it is a non-contact processing itself. It does not need to consider the hardness of the material, but only needs to ensure that the material has sufficient light absorption capacity. By cutting the surface holes and peripheral contour of the hot formed plate, the structure and size of the product are well guaranteed, and the processing efficiency is particularly high.
For ordinary plane structures, three-dimensional plane cutting equipment can be used. For equipment with complex structure, robot laser cutting can be used; For single robot cutting, it is difficult to ensure the roundness of small circles, and professional three-axis auxiliary cutting is required; For parts with complex structure and high precision requirements, three-dimensional five axis laser cutting equipment is required.
Figure 2 Application Structure Description of Automobile Hot Formed Sheet
The structure used for hot forming processing on the automobile is shown in Figure 2, including transverse support beam, mounting bracket, door panel reinforcement, roof side member, window reinforcement, rear bumper, middle pillar (B pillar), door sill, front pillar (A pillar), longitudinal bearing beam, front bumper and floor passage.
After the hot forming process, the strength of the sheet metal is significantly improved, and it is difficult to achieve the effect of the traditional stamping process by using the ordinary stamping process. Through 3D cutting, it can realize the cutting of the outer contour and inner hole of the structural part, non-contact processing, high efficiency, good precision, smooth cut surface and stable cutting process. Hot forming and matching laser cutting technology is a solution that can achieve weight reduction only by changing the material process.
B-Pillar Cutting System with 3D Laser Cutting Machine
The solution of Farrell to solve the cutting of B pillar hot formed parts is shown in Figure 3. A complete set of B pillar cutting, including the external contour and internal holes, can be completed within 50 seconds, and the accuracy can be controlled within 0.01 mm.
2. Laser panel welding
Laser panel welding (see Figure 4) can weld materials with different strength levels, different thicknesses, and different coatings together (see Table 2), and conduct overall stamping forming. It can optimize material selection, reduce parts and molds, save manufacturing costs, improve the overall stiffness of parts, and provide better safety performance. It is one of the main technologies for current automobile lightweight.
B pillar laser welding system
Table 2 Material combination of laser tailor welded automobile steel
The characteristics of laser tailor welded blanks (see Figure 5) are high welding heat input, no filler, no overlap, fast speed, large penetration, small deformation, small heat affected zone and grain refinement of weld heat affected zone.
Fig. 5 Improvement description of laser panel of car front longitudinal beam
1) The volume of the weld zone is reduced, the weld height is not increased, the joint is flat, and the thermal stress concentration of the geometric shape is small.
2) The weld heat affected zone is narrow, the grain is fine, the weld strength is high, and the impact on the stamping forming characteristics is small.
3) Welding automation, high productivity, neat production workpiece, consistent quality.
4) The online detection can ensure the quality of the weld and the accuracy of the geometric dimension, and each TWB can be accurately tracked and controlled.
The factors affecting the quality of tailor welded blanks mainly include butt gap, laser spot mode, laser power, welding speed and gas shielding.
As the diameter of laser spot is generally less than 0.5mm, if the butt gap is too large, the laser will directly penetrate and cannot effectively heat the sheet metal, resulting in welding failure; At the same time, due to the influence of tooling and fixtures, there will be a gap when two sheets butt.
Taking the plate thickness t as a reference, the research on equal thickness butt welding of DP600 dual phase steel shows that when the butt gap is less than 0.18t, the obtained weld has no obvious defects, and when the butt gap is less than 0.16t, the weld strength is higher than the base metal. In engineering application, when t is 0.5~3mm, the butt gap should be less than 0.1t; When t is 3~10mm, the butt joint clearance shall be less than 0.05t. For 2mm thick mild steel, the butt clearance shall be less than 0.12mm< span="">
3. Door laser welding application
The laser welding structure of the door is shown in Figure 6a, which is the welding of the window frame and the inner plate. The weld is a red line segment. The actual object is shown in Figure 6b on the right.
Fig. 6c For the width requirements of the flanging structure corresponding to the flanging structure for spot welding and laser welding, the flanging size for laser welding is required to be 6~8mm, and the flanging size for spot welding is required to be 15~18mm.
Figure 6 Comparison of door structure flanging size design (spot welding and laser welding)
c) Width requirements of flanging structure
If laser welding is used instead of spot welding, the flanging size can be reduced by 8~10mm. The total length of the door and side wall is calculated as follows.
Figure 7 Calculation of side wall flanging size
Simply calculate the effect of reducing the flanging size of the side wall and welding the overlapped metal plate on the lightweight. Calculation result: 14 200mm flanging length at left, right, front and back × Reduction of 6mm flanging × 2mm plate thickness, that is, the total mass is reduced by 1.86kg, about 4%.
Figure 8 Comparison of Door Laser Weld Structure Flanging (Lap and Overlap Welding, Structure and Object)
As shown in Figure 8, the entrance is increased. Take column A as an example. If overlap welding is changed to overlap welding, it is estimated that the flanging size will be reduced by 12 mm in width and height, and the final weight will be reduced by about 8%.
4. Laser welding of aluminum alloy
Aluminum alloy is a popular lightweight material at present. The research shows that the fuel consumption can be reduced by 37%, the load of the suspension device can be reduced by 18%, and the vibration intensity can be reduced by 5% by using aluminum alloy materials to properly reduce the mass of the vehicle.
The proportions of materials, body in white quality and corresponding body connection processes of Cadillac CT6, Audi A8, Jaguar XFL, Weilai ES8 and Tesla Model S models are compared as follows.
In addition, when the proportion of Tesla Model S aluminum alloy is increased from 61% to 90%, the body mass is reduced from 450kg to 338kg, and the weight loss is 112kg, with a weight loss ratio of 25%.
The length of laser weld is 30m on German Volkswagen Audi A2 car with all aluminum structure; Laser welding technology is widely used on the body of its multi-function car, with a total length of 41m.
The body structure adopts aluminum alloy laser welding, mainly focusing on the connection between the top cover and the side wall, the upper and lower plates of the rear cover outer plate, as well as some door inner plates and stiffeners, and the inner and outer plates of the side wall.
The main materials used are aluminum alloy 5 series (i.e. 5000, referred to as "5 series", the same below) and 6 series, which have excellent mechanical properties and welding properties; The defects that are easy to appear in aluminum alloy laser welding are mainly air holes and cracks. For Series 5 and 6, swing laser welding is used when wire is not filled, and the laser head with stable smooth wire is used for wire filling welding. The problem of weld formation and defects can be well solved by filling Series 4 wire.
Table 3 Aluminum Alloy Application Comparison and Connection Process Description of Several Typical Lightweight Vehicles
The steel aluminum mixture is a feasible solution. The connectivity of steel aluminum will be more and more applied to the actual body structure in the lightweight propulsion process.
Leave a Comment