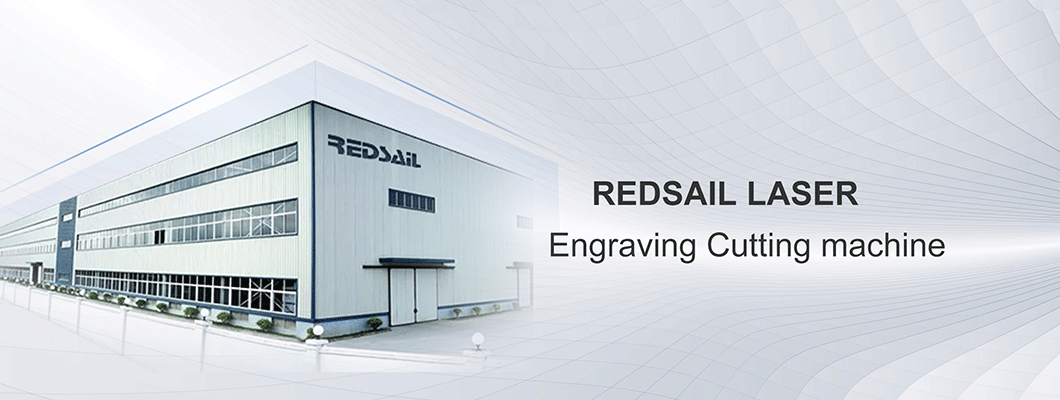
At present, China's traditional manufacturing industry is facing profound transformation and upgrading, and high-end precision machining with high added value and high-tech barriers is one of the important directions. With the increasing demand for high-precision machining, the related precision machining technology has also developed rapidly, and laser technology is increasingly recognized in the market.
The laser processing technology can be divided into three levels according to the size and accuracy of the materials to be processed: it is mainly the laser processing technology for large materials composed of medium and thick plates, and the processing accuracy is generally in the millimeter or submillimeter level. Precision laser processing technology is mainly aimed at thin plates, and its processing accuracy is generally about 10 microns. Based on various thicknesses less than 100 μ The laser micromachining technology of m thin films is usually lower than 10 microns or even sub microns. Today, we mainly introduce precision laser processing.
Laser precision machining can be divided into four types of applications, namely precision cutting, precision welding, precision drilling and surface treatment. In the current technological development and market environment, the application of laser cutting and welding is more and more popular, and 3C electronics and new energy batteries are the most widely used fields.
Laser precision cutting
Laser precision cutting uses a pulsed laser beam to focus on the surface of the processing object to form a light spot with high energy density. The light spot melts or vaporizes the processing material at an instantaneous high temperature. Its processing characteristics are high speed, smooth and flat cut, usually without subsequent processing; The cutting heat affected zone is small, and the plate deformation is small. High machining accuracy, good repeatability, and will not damage the material surface.
Compared with high-power laser cutting, precision cutting usually uses nanosecond and picosecond lasers according to the processing object, which can focus on the ultra-fine spatial area. At the same time, it has very high peak power and very short laser pulses. In the process of precision cutting, the surrounding materials within the space involved will not be affected, so as to achieve "super fine" processing. In the production process of mobile phone screen cutting, fingerprint identification, LED invisible cutting, high precision is required, and laser precision cutting technology has incomparable advantages.
Laser precision welding
Laser precision welding radiates high intensity laser beam to the working area of processed products. Through the interaction between laser and material, the welding position can quickly form a multi density concentrated heat source area. The heat will melt the area to be welded and then cool the crystals to form a solid weld. It is characterized by no need for electrodes and filler materials, and non-contact welding. Welding of high melting point refractory metals or materials of different thicknesses.
In the field of new energy batteries, with the promotion of new energy vehicles, the demand for power batteries continues to grow. Laser welding is used as the standard equipment in the field of power battery. It is widely used for welding the front pole, the bottom cover in the middle, the top cover and the sealing nails, as well as the rear battery connecting piece and the negative pole seal. In the 3C field, all types of mobile phone modules and middle plate covers are inseparable from laser precision welding technology.
Laser precision drilling
Laser precision drilling is to reduce the spot diameter to micrometer level to obtain high laser power density. It can be carried out on almost any material. It is characterized by small hole diameter, fast processing speed and high efficiency, which can be drilled on high hardness, brittleness or soft materials.
Laser drilling is the most widely used technology in PCB industry. Compared with traditional PCB drilling technology, laser drilling on PCB not only has faster processing speed, but also can drill holes less than 2 μ M small holes, micropores and invisible holes, which can not be realized by traditional equipment. On the surface of electronic products, it can also be used to drill holes in mobile phone speakers, microphones and other glass.
Laser surface treatment
Laser surface treatment refers to the use of high power density laser beam for surface treatment of metals, which can achieve phase transformation hardening, surface amorphization, surface alloying or cause surface materials to vaporize or change color, thus changing the chemical reaction surface properties of metal materials. Its characteristic is that it does not need to use other materials, but only needs to change the structure of the surface layer of the treated materials. The processed parts have the minimum deformation, and are suitable for surface marking and high-precision parts processing.
According to whether the composition of the substrate changes, laser surface treatment can be divided into two categories. Applications that do not change the composition of the substrate include laser hardening (phase transformation hardening), laser cleaning, laser shock hardening, and laser polarization. Applications that change substrate composition include applications such as laser classification, laser cladding, laser alloying, and laser vapor deposition.
Leave a Comment