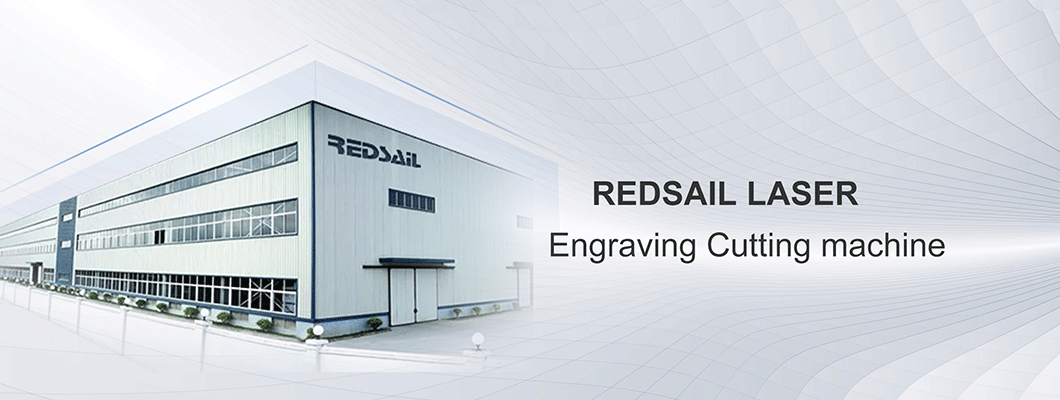
Laser has good monochromaticity, coherence and parallelism, so it is especially suitable for material processing. Domestic traditional pipe cutting methods mainly rely on manual sawing, sawing machine sawing, roller extrusion, grinding wheel cutting, gas welding cutting, etc. these processing methods basically have shortcomings such as low cutting efficiency and high labor intensity of workers, while laser cutting is widely used in industrial fields with its advantages such as fast processing efficiency and good processing effect.
With the development of science, technology and industry, pipes have been widely used to manufacture parts in aircraft manufacturing, engineering machinery, transportation, petrochemical industry, agricultural machinery and other industrial sectors. In actual production, pipe has the advantages of low production cost, good processing formability, light weight of structural parts and saving materials, so pipe cutting has a very important position in the industrial field. Due to the different shapes, sizes and applications of pipes, and the pipe cutting is restricted by processing quality and other factors, it is very important to select reasonable processing equipment, processing methods and technological measures.
There are many inconveniences in pipe cutting, and although the traditional cutting methods in China can achieve the application effect, the processing efficiency is low and the processing effect is poor. Therefore, combining pipe cutting with laser technology will make the pipe cutting field have a broader development prospect.
Present situation and future development of pipe laser cutting
Laser cutting pipe has many advantages, such as narrow cut width, small heat affected zone, fast cutting speed, good flexibility, smooth cut and no tool wear. With the emergence and development of numerical control laser pipe cutting machine, the development of various processing technologies for spatial free-form surfaces and curves can show its unique side. When cutting pipes by laser, it is not only required that the laser spot moves along a certain trajectory in the three-dimensional space relative to the workpiece, but also that the laser optical axis is always perpendicular to the processing surface of the pipe to be cut in the whole processing process. For the NC fiber laser cutting head that can automatically focus, the nozzle can automatically track the workpiece surface through the automatic measurement and control system. The production practice shows that the key of pipe cutting is to eliminate the cutting quality defects to the greatest extent, so as to meet the processing requirements of pipes. Laser cutting is not only faster than traditional processing methods, but also can greatly guarantee the processing quality when complex pipes are processed such as punching, slotting, edge cutting or side concave.
Overview of pipe laser cutting
In the process of processing, first of all, the pipe parts should be cut to obtain the required length of pipe blanks. Domestic traditional pipe cutting methods can hardly meet the needs of mass production, and the processing quality of the cut surface of pipe parts processed by these traditional processing methods is generally poor, and some even have processing defects such as deformation and collapse. In addition to cutting, some pipes also need other forms of processing, such as pattern cutting for decoration and lamps, spiral, sine and cosine cutting, marking, etc. If the traditional processing method is used in these forms of pipe processing, not only the processing efficiency is low, but also it is difficult to meet the ideal processing requirements, and some of them can not be processed.
Advantages of tube laser cutting
When cutting pipes by laser (including tangent, beveling, forming cutting, etc.), the cutting width is generally 0.1 ~ 0.3mm, and the cutting position and temperature can be accurately controlled, which is more conducive to the automation and intelligence of production. Compared with the traditional processing method, the cutting efficiency can be increased by 8 ~ 20 times, the processing cost can be reduced by 70% ~ 90%, and the material loss can be saved by 15% ~ 30%. Moreover, the noise of laser cutting is small, and the impact on the environment is small. The traditional processing method requires multiple continuous processes to complete the processed parts, which can be realized on the same equipment by laser cutting. With the continuous improvement of equipment performance and processing technology, it is possible to use laser to cut pipes with high quality.
Future development trend of pipe laser cutting
The laser cutting adopts a non-contact processing method, which will not exert any pressure on the pipe wall during the whole processing process, so it will not cause deformation or collapse of the outer surface of the pipe. At the same time, when laser cutting pipes, the complicated thermal field in the slit, the difficulty in cooling, and the easy blockage of cutting slag make it more difficult to cut. Therefore, it is necessary to strengthen the in-depth research on these aspects.
Laser cutting has a great degree of freedom for the material, shape, size, processing environment and other requirements of pipes. It has excellent spatial controllability (beam direction change, rotation, scanning, etc.) and time controllability (on, off, pulse interval) and is easy to control. Moreover, because of the high precision and less burr of laser cutting, the time consumed for subsequent processing is greatly reduced. When changing the diameter or shape of the pipe, it only needs to modify the program, so the development of the pipe cutting software is of great research value. The combination of laser cutting system and computer numerical control technology can form high-efficiency automatic equipment and open up a new way for high-quality, high-efficiency and low-cost processing.
In order to improve the working efficiency of pipe cutting, the most effective production method is to use the automatic production line of pipe laser cutting. How to use the automatic pipe cutting production line for laser cutting? First, the focused laser beam must be synchronized with the cut pipe on the automatic pipe cutting production line; Secondly, it is required that the laser focus after focusing can rotate one circle relative to the pipe to be cut, and the axis of the laser beam is always perpendicular to the axis of the pipe. During the cutting process, the laser beam of the pipe cutting production line moves with the pipe to be cut. These synchronous movements must be controlled by a special control system, so it is also of great significance to study the automatic production line of pipe laser cutting.
Key technology of pipe laser cutting
Light guide focusing system
In the laser cutting equipment, the function of the light guide system is to guide the light beam output by the laser generator to the cutting head of the focusing optical path. For laser cutting pipes, to obtain high-quality slits, it is necessary to have a small focus spot diameter and high power of the focused beam, which makes the laser generator output low-order modes.
When laser cutting pipes, in order to obtain a relatively small beam focusing diameter, the transverse mode order of the laser is small, and it is better to use the fundamental mode. The cutting head of the laser cutting equipment is equipped with a focusing lens. After the laser beam is focused by the lens, a small focusing spot can be obtained, so that high-quality pipe cutting can be carried out.
Trajectory control of cutting head
In pipe cutting, the pipe to be processed belongs to spatial curved surface, and its shape is relatively complex. If it is programmed and processed by conventional methods, it will be difficult. This requires the operator to select the correct processing path and appropriate reference point according to the processing process requirements, record the feed of each axis and the coordinate value of the reference point by using the CNC system, and then use the spatial straight line and arc interpolation function of the laser cutting system, Record the coordinate values of the machining process and generate the machining program. Therefore, the research on the automatic vertical function of laser beam and pipe cutting is also one of the important technical contents of pipe laser cutting.
Automatic control of laser cutting focus position
In order to ensure the cutting quality of laser cutting pipes, the vertical direction of the focus relative to the workpiece surface can be kept constant through automatic measurement and control devices, which is the key of laser cutting pipes. At present, through the integration of the control of the laser focal position and the linear axis (X-Y-Z) of the laser processing system, we make the movement of the laser cutting head more light and flexible, and we can know the focal position like the palm of our hand, so as to avoid the collision between the cutting head and the cutting pipe or other objects in the processing process.
Influence of main process parameters
The application of laser cutting pipes in today's industrial society is more and more extensive, the pipes to be cut are more and more diverse, and the pipe parts themselves have their own complexity. Therefore, according to the material, shape and processing requirements of the cut pipes, selecting the appropriate laser cutting process parameters to obtain the best cutting efficiency and quality has become the most concerned problem of all users of the laser cutting system.
(1) influence of optical power.
For the continuous wave output laser generator, the laser power will have an important impact on laser cutting. Theoretically, the higher the laser power of the laser cutting pipe equipment, the higher the cutting speed can be obtained. However, considering the characteristics of the pipe itself, the maximum cutting power is not the best choice. When the cutting power is increased, the mode of the laser itself will also change, which will affect the focusing of the laser beam. In actual processing, we often choose to let the focus get the highest power density when the power is less than the maximum power, so as to ensure the efficiency and quality of the whole laser cutting.
⑵ influence of cutting speed.
When laser cutting pipes, it is necessary to ensure the cutting speed within a certain range in order to obtain better cutting quality. If the cutting speed is too slow, too much heat will accumulate on the surface of the pipe, the heat affected zone will become larger, the slit will become wider, and the discharged hot melt material will burn the surface of the incision, making the surface of the incision rough. When the cutting speed is accelerated, the average circumferential slit width of the pipe becomes smaller, and the smaller the pipe diameter is cut, the more obvious this effect is. With the acceleration of cutting speed, the time of laser action is shortened, the total energy absorbed by the pipe becomes less, the temperature at the front end of the pipe decreases, and the slit width decreases. If the cutting speed is too fast, the pipe can not be cut through or can not be cut, thus affecting the whole cutting quality.
(3) influence of pipe diameter.
When laser cutting pipes, the characteristics of the pipes themselves will also have a great impact on the processing process. For example, the size of round pipe diameter has a significant impact on the processing quality. Through the research on laser cutting thin-wall seamless steel pipe, it is found that the laser cutting pipe equipment will continuously increase the pipe diameter and the slit width under the condition that all process parameters remain unchanged.
⑷ type and pressure of auxiliary gas.
Compressed air or inert gas (such as nitrogen) can be used as auxiliary gas when cutting nonmetal and part of metal pipes, while active gas (such as oxygen) can be used for most metal pipes. After determining the type of the auxiliary gas, it is also very important to determine the pressure of the auxiliary gas. When cutting pipes with small wall thickness at a higher speed, the pressure of auxiliary gas should be increased to prevent slag from hanging on the notch; When the cutting pipe wall thickness is large or the cutting speed is slow, the pressure of the auxiliary gas should be appropriately reduced to prevent the pipe from being cut through or cut continuously.
When laser cutting pipes, the position of beam focus is also very important. When cutting, the focus position is generally on the surface of the cutting pipe. When the focus is in a good position, the slit is the smallest, the cutting efficiency is the highest, and the cutting effect is the best. In most cases, the beam focus is adjusted below the nozzle, and the distance between the nozzle and the pipe surface is about 1.5mm. At the same time, laser pulse waveform, light output mode and other factors also have a certain impact on the cutting effect.
Concluding remarks
Laser cutting of pipes can not be separated from the support of hardware laser cutting system (including laser generator) and software laser cutting technology. From the perspective of hardware, the future laser tube cutting opportunities will develop in the direction of high speed, high precision, high automation, flexibility and diversified functions; From the perspective of software, the future laser cutting will be continuously combined with numerical control technology to develop new software. Therefore, the collection and collation of laser cutting process data and the establishment and improvement of expert system are of great significance and research value to the development of the whole laser cutting industry.
Leave a Comment