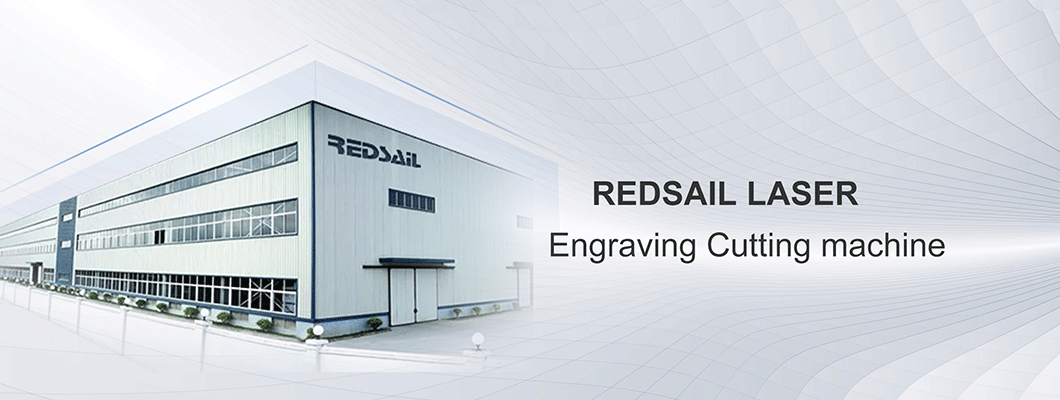
The stent belongs to the third category of medical devices, that is, the highest level of medical devices. It is a slender metal grid, very small, 2-4 mm in diameter, a few centimeters long, hollow, cylindrical, mesh metal tubes. The smallest diameter of the imported stent is 2.25 mm, while the smallest diameter of the domestic stent is 2.5 mm. The imported stent has certain advantages in small blood vessels.
To put it simply, the principle is to "put a tiny stent into the blood vessel, stretch the narrow part, and keep the blood flow in the lumen smooth. At present, the stent has a variety of products such as medical stainless steel, nickel titanium alloy, magnesium titanium alloy, cobalt chromium alloy, soluble metal magnesium and biodegradable polymers; according to the placement position, it can be divided into coronary stent, cerebrovascular stent, renal artery stent, large artery stent, etc.
One of the most lucrative commodities in the world
In the vascular stent industry, it is praised as "the pearl on the crown of medical devices" A blood vessel stent, which is smaller than the nail plate, often sells for tens of thousands of yuan, with a gross profit margin of more than 90%, which is much more expensive than mobile phone chips. At present, in the world, vascular stents are mainly monopolized by Abbott, Boston Scientific, Medtronic and other giants. In China, there are mainly three companies involved, namely, minimally invasive medical, Lepu Medical, and Jiwei Medical (a subsidiary of Parsons).
There are some reasons why it is so expensive:
First, the low innovation ability of domestic supports makes the import price subject to others. There are few medical devices with independent intellectual property rights in China, and most of them are just copying foreign technologies.
Second, there are many circulation links, resulting in price increases at different levels. The medical supplies market in the United States is a direct marketing model, while China is an agency model. There are many levels of the overall supply chain, which inevitably leads to high prices after the products arrive at the terminal.
Third, the R&D profit of the scaffold is low, and the enterprise enthusiasm is not high. On the one hand, there are technical limitations. Because cerebrovascular diseases are complex and risky, small hospitals are unable to perform stent surgery, which limits the market demand. On the other hand, the market is monopolized, the R&D investment is large and the profit space is small, and the enterprises lack R&D enthusiasm.
How are vascular stents manufactured?
Because the wall tube of the cardiac stent is extremely thin, the current mainstream stent cutting uses microsecond fiber laser. However, since laser processing itself is hot processing, melting the metal with laser and blowing it away with high-pressure gas will not only leave a lot of molten slag and burrs after processing, but also the heat during processing will easily oxidize the surface layer of the support to make it brittle, and the residual thermal stress will also cause microcracks and reduce the mechanical properties. And the processed support needs a series of post-treatment, including cleaning, grinding, pickling, passivation, and the final electrochemical polishing, which is tedious and time-consuming. These subsequent treatments will also lose some of the supports. The final yield is only about 70%, and about 30% of the losses mean huge losses.
In recent years, domestic and foreign enterprises have begun to use a new technology for bracket cutting, ultra fast laser, or ultra short pulse laser. Its pulse width is only 10 picoseconds (10-12 seconds) to hundreds of femtoseconds (10-15 seconds), which can achieve "cold" processing without thermal effect. Different from the melting mechanism of microsecond laser, the extremely high peak power brought by the ultra short pulse width of ultrafast laser will produce multiphoton absorption, which will directly evaporate the material through the melting process. Therefore, ultrafast laser can process materials with relatively low energy, without residual heat and residue left on the materials, achieving high-precision and clean processing, and many subsequent processes can be omitted. Generally speaking, the cleaned bracket can be electrochemical polished directly; Due to the simplification of the manufacturing process, the yield can be increased to more than 90%.
Leave a Comment