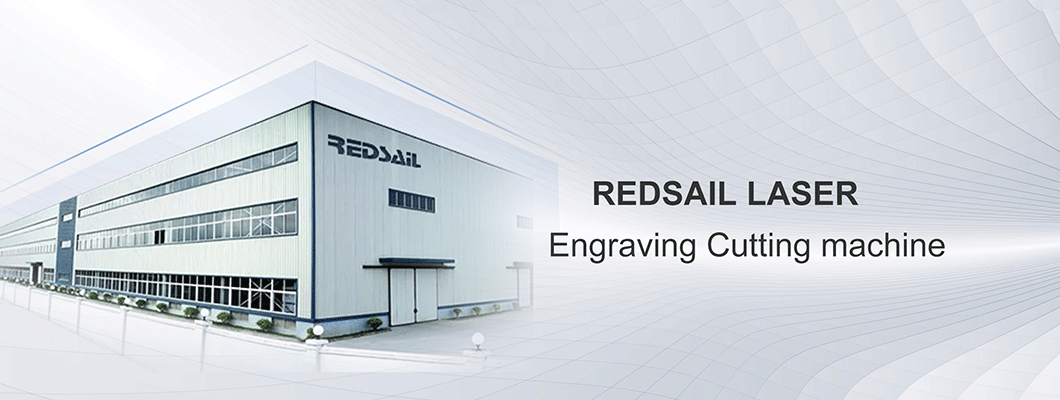
Due to the special use environment of medical equipment, we have special requirements for its accuracy, safety, smoothness and sanitary conditions. Therefore, when manufacturing medical devices, manufacturers must be strictly required from the source. In the process of metal medical equipment processing, the traditional sheet metal mechanical cutting processing method has great shortcomings in accuracy, safety and controllability. It is an inevitable trend of industrial development to replace traditional processing methods with optical fiber laser cutting machines
First of all, laser cutting can meet the requirements of the medical community on precision, safety and finish. Optical fiber laser cutting uses a high power density laser beam to scan the surface of materials, and heats the materials to thousands to tens of thousands of degrees Celsius in a very short time, thus melting or vaporizing the materials. Then, high pressure gas is used to blow the melted or gasified materials away from the slit to achieve the purpose of cutting materials. Such high temperature ensures the possibility that the instrument will not be polluted twice during processing. In addition, the cutting surface finish of the processed materials is very good, which can meet the requirements of one-time molding, and avoid the loss of time and materials caused by two or more processing after molding.
Secondly, from the perspective of the workpiece itself, medical equipment is very different from other mechanical parts. It requires very high accuracy without any deviation, and the laser cutting machine can well meet these processing requirements when cutting equipment.
In addition, the cutting slit produced by laser cutting is very narrow, and the laser beam is focused into a small spot, so that the focus reaches high power density, the material is rapidly heated to the extent of vaporization, and the hole is formed through evaporation. With the relative linear movement of the light beam and the material, a narrow slit is continuously formed in the hole, and the width of the slit is usually 0.10-0.20mm. The tiny slit ensures high cutting accuracy.
The production process of laser cutting machine is non-contact. The laser cutting head will not contact the surface of the material to be processed and will not scratch the workpiece. For medical devices, surface smoothness is the most basic requirement. If the surface grinding process of equipment products can be minimized during processing, the production efficiency will be greatly improved.
Leave a Comment