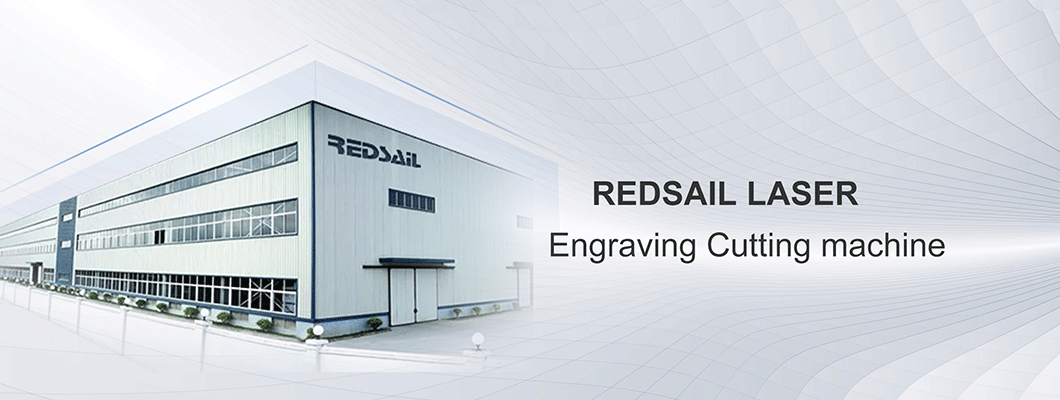
Burr is a common phenomenon in the process of processing metal materials by optical fiber laser cutting machine. It is shown on various irregular metal parts at the transition point of the workpiece surface, such as acute angle, burr, etc. However, the appearance of burr does not mean that the appearance of burr directly affects the dimensional accuracy, shape and position accuracy and surface roughness of the workpiece, and reduces the quality of the product. This brings many problems to the subsequent inspection, assembly, performance and aesthetics, so burrs should be avoided as much as possible.
Is the burr produced by laser cutting a quality problem of the cutting machine?
When many enterprises use the laser cutting machine for cutting, they find that the cutting burrs of the workpiece are many and the quality is not ideal. Therefore, they suspect that the quality of this cutting machine has problems. Is this really why? not always. In most cases, the burr is not caused by the quality problem of the laser cutting machine itself, but by the wrong operation mode of the operator or the inadequate maintenance of the cutting machine.
In addition, there is also a major reason for burrs, that is, the problem of auxiliary gas. When laser cutting, the laser beam irradiates the surface of the workpiece to produce a very high temperature, which makes the surface of the workpiece evaporate, so as to achieve the purpose of cutting metal. The role of the auxiliary gas is to blow out the residual slag on the surface of the workpiece after the workpiece is irradiated and evaporated by the laser beam. If this is not done, a layer of adhesive burrs will form on the cutting surface of the workpiece when the slag is cooled.
Next, let's summarize the causes of several common burrs and the corresponding solutions to help readers stay away from the problem of laser cutting burrs.
Common causes and solutions of laser cutting burrs:
Cause 1: The laser cutting machine produces the deviation of the upper and lower positions of the laser beam focus, which causes that the energy is not completely concentrated on the workpiece, the workpiece is not fully vaporized, the slag output increases, it is difficult to blow off, and it is easy to produce burrs.
Solution: Adjust the position of the laser beam focus to the best state according to the offset position.
Reason 2: The output power of the laser cutting machine is insufficient, and the metal cannot be effectively evaporated, resulting in a large number of slag and burrs. Solution: Check whether the laser cutting machine works normally. If not, timely repair and maintenance are required; If it is normal, check whether the output value is correct.
Cause 3: The cutting line speed of the laser cutting machine is too slow, which destroys the surface quality of the cutting surface and produces burrs.
Solution: Adjust and increase the cutting line speed in time to make it reach the normal value.
Reason 4: The purity of the auxiliary gas of the laser cutting machine cannot meet the required standard, which will also cause the workpiece to burr.
Solution: Replace the high-purity auxiliary gas.
Cause 5: The working time of the laser cutting machine is too long, which makes the equipment unstable and also leads to burrs.
Solution: Turn off the laser cutting machine, restart and move it after a period of time, so that it can have a full rest.
The above are several common causes and solutions for burrs. Only by understanding the root causes of the problem can we effectively solve the problem. It is hoped that readers and friends engaged in machining and sheet metal processing can better grasp the processing details, improve product quality and jointly promote the progress of China's manufacturing industry.
Leave a Comment