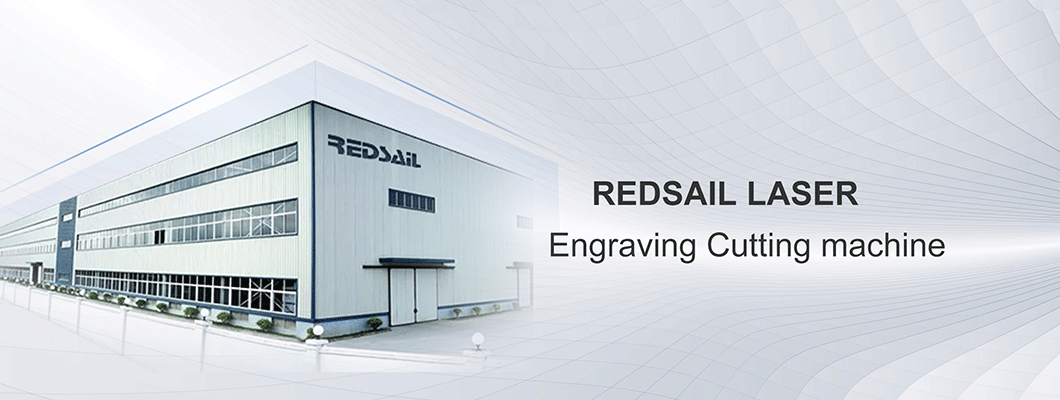
With the increasingly fierce competition in the laser processing industry, how to improve efficiency and reduce costs has become the concern of most users. With the advantages of fast cutting speed, small material deformation and high processing accuracy, optical fiber laser cutting machine has quickly become the mainstream of the market. The application of high-power laser has greatly improved the efficiency of laser processing. The limit cutting speed of thin plate has been able to challenge the control limit of mechanical properties, and the cutting process of medium and thick plate is also constantly breaking through.
The commonly used cutting auxiliary gases for fiber laser cutting machine include oxygen, nitrogen and air. However, since the cost of nitrogen and oxygen is higher than that of compressed air, and the price of nitrogen and oxygen increases year by year, using air as cutting auxiliary gas can greatly reduce the production cost.
Oxygen is mainly used for carbon steel cutting. Its principle is that oxygen reacts with metal to produce a large amount of oxidation heat. At the same time, certain air pressure will blow out oxides and slag from the reaction zone, forming a cut in the metal. Because the oxidation reaction in the cutting process produces a lot of heat, it does not need too high power, but the cutting tip is easy to burn.
Nitrogen is mainly used for cutting stainless steel and aluminum plates, and can also cut carbon steel plates of certain thickness. The higher the power, the greater the thickness of carbon steel plates that can be cut. Nitrogen cutting relies on the energy of laser to melt the metal, and high pressure blows away the molten material to avoid unreasonable chemical reaction. In stainless steel and aluminum plate cutting, you can get a brighter section effect, and the sharp corner effect is also better.
The air itself exists in the atmosphere. It is compressed to the air storage tank by the air compressor, and then filtered, cooled and dried to remove the water and oil in the air before use. The cutting principle of air is similar to that of nitrogen, but since the air contains about 20% oxygen, it can make up for the shortage of oxygen and nitrogen to a certain extent.
In terms of cutting speed, air has no advantage over nitrogen, but they are far higher than oxygen in the thickness of 8mm and below. Of course, the brightness and bottom finish of carbon steel section cut by oxygen will be better than that of air and nitrogen.
In comprehensive consideration, under the relatively loose requirements, air cutting has a large cost advantage. However, it should be noted that when air cutting is used, it must be ensured that the air is filtered by the cold dryer, and the air compressor and cold dryer need regular maintenance. If the air entering the cutting head contains water and oil, it will cause fog on the protective lens in a short time and affect the cutting quality. At this time, if the protective lens is not replaced in time, the internal temperature of the cutting head may also rise under the irradiation of high power beam, which may cause damage to the internal lens group.
For factories with large processing capacity, air cutting with high power cutting machine can bring higher efficiency and lower cost, which is far higher than the cost of secondary processing of workpieces. However, for small processing plants, air cutting may not reduce costs. Therefore, whether to use air cutting needs to be determined according to its own production.
Leave a Comment