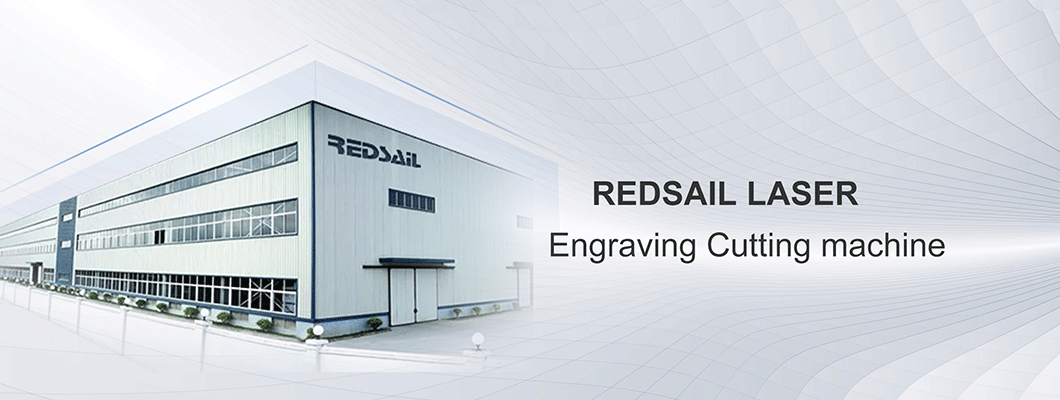
In the daily batch processing of steel plate, after continuous processing, the processing quality of the sheet metal laser cutting machine will become worse. We discuss the causes and solutions based on the setting of processing parameters.
1. Slag adhered after a period of treatment. The main reason is that molten metal cannot be discharged from the slit. The possible causes are the optical path problem of the laser head, the change of cutting gas flow and the change of plate temperature after processing. At this point, we can compare the gap width between the descending part and the non descending part. If the slit width is different, it means that the cutting head lens is dirty, which leads to the deviation of the actual focus position and the laser center.
Clean and disassemble the lens in a dust-free environment. Observe the laser output head with a 20X microscope, and then wipe it with a dust-free cotton swab and absolute alcohol.
Do not remove optical parts without the relevant permission or removal conditions.
2. Excessive combustion after long-time processing.
When the thick plate is processed for a long time, the processing speed is relatively slow. Because the heat accumulation of the plate causes the material temperature to rise, this phenomenon may lead to excessive combustion.
(1) If the nozzle is abnormal or overheating, check the inner lens.
(2) Use white paper to observe the red light, make it far away from the nozzle or tilt at a certain angle. If there is obvious shadow in the red light, it means that the internal lens is dirty.
(3) The most intuitive judgment method is to observe the optical fiber output head with a microscope in a dust-free room, and observe whether there is any abnormality inside the two ends of the cutting head.
Leave a Comment