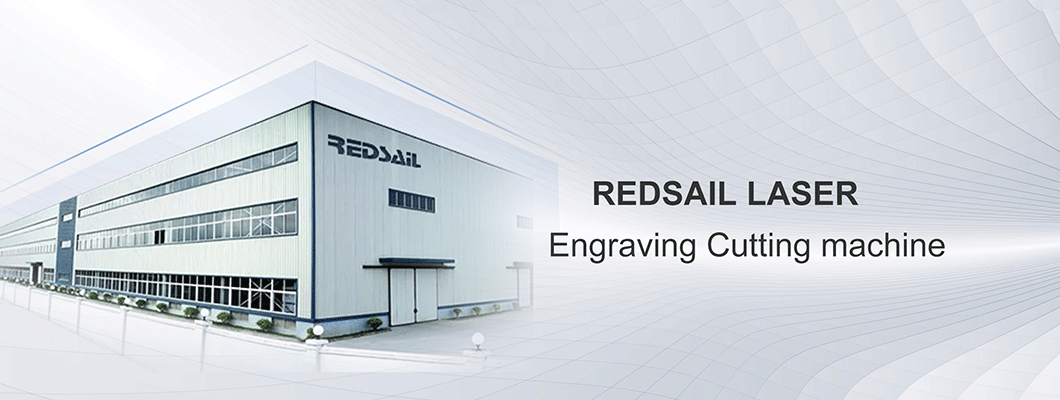
Laser cutting machine has the advantages of wide cutting range, fast cutting speed, narrow cutting, etc. It is widely used in automobile manufacturing, kitchenware industry, sheet metal processing, advertising, machinery manufacturing, chassis cabinet, elevator manufacturing, fitness equipment and other industries. Joint, good cutting quality, small heating area, flexible processing.
What is the cutting thickness of the laser cutting machine?
At present, the cutting thickness of laser cutting machine is generally less than 25mm. Compared with other cutting methods, it has obvious advantages when cutting materials with dimensions less than 20 mm. However, failure to follow proper safety control methods can also lead to personal injury or machine damage.
At present, many manufacturers' machines have realized automatic focusing. Among them, high-power CO2 laser and YAG laser are widely used in processing. Fiber laser based on fiber bit matrix has significant advantages in reducing threshold, oscillating wavelength range, wavelength tunable function, and has become a new technology in the laser field. With the help of the auto focusing function, the processing efficiency of the laser cutting machine can be significantly improved: the perforation time of thick plates is greatly reduced; When processing workpieces of different materials and thicknesses, the machine can automatically adjust the focus to the most appropriate position.
Common problems of laser cutting machine?
What are the types of lasers and what are the differences between them?
At present, the lasers used for laser processing and manufacturing mainly include CO2 lasers, YAG lasers and fiber lasers. Compared with ion cutting and oxygen cutting, laser cutting produces less dust, weaker light and lower noise.
What are the factors that affect the accuracy of laser cutting machine?
There are many factors that affect the accuracy of laser cutting, some of which depend on the equipment itself, such as the accuracy of the mechanical system, the impact degree of the workbench, the quality of the laser beam, the influence of auxiliary gas and nozzle, etc. Some of them are inherent factors of materials, such as physical and chemical properties of materials, reflectivity of materials, etc; Some of them are selected according to the detailed processing objects and user's quality requirements, making corresponding adjustments to determine relevant parameters, such as output power, focus position, cutting speed and auxiliary gas.
During the operation of the machine, the operator shall not leave without authorization to avoid unnecessary losses. The spot size after laser beam extraction is proportional to the focal length of the lens.
Laser cutting is a thermal cutting method, which uses focused high power density laser beam to irradiate the workpiece to melt, vaporize, ablate or reach the burning point of the materials in the irradiated area, and then blow out the molten materials through the laser. The high-speed airflow is coaxial with the beam, and the point irradiation position is moved through the numerical control mechanical system to cut the workpiece.
Do not store explosives in explosives. It is forbidden to observe the laser through binoculars, microscopes, magnifiers, etc. It is not allowed to cut certain materials on the laser cutting machine, including foam core materials, any PVC materials, high reflective materials, etc.
Leave a Comment