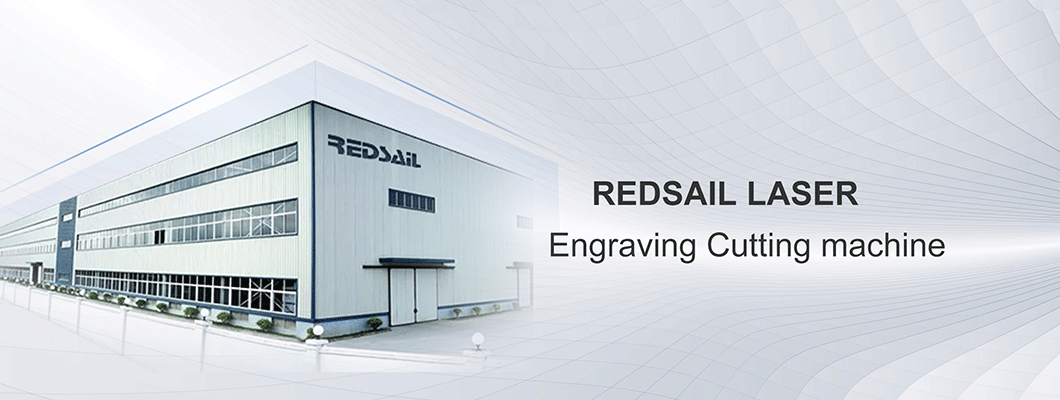
When the cutting quality of the optical fiber laser cutting machine is poor, it is recommended to carry out a general inspection first. The inspection contents and sequence are as follows:
1. Cutting height: it is recommended that the actual cutting height be between 0.8 and 1.2mm. If the actual cutting height is not accurate, it needs to be calibrated;
2. Check whether the model and size of the cutting tip are used incorrectly, whether the cutting tip is damaged and whether the roundness is normal;
3. Optical center: it is recommended to use a cutting tip with a diameter of 1.0 for optical center inspection, and the focus is between - 1 and 1, so that the light spot produced is small and easy to observe;
4. Protect the lens and check whether the lens is clean and free of water, oil and slag. Sometimes the protective lens may be fogged due to weather or paving gas;
5. Focus inspection: check whether the focus is set correctly. If these five items are all checked without problems, then modify the parameters according to the phenomenon.
Common phenomena and parameter adjustment:
(1) Cutting stainless steel slag hanging: there are many types of slag hanging. For example, if only hanging slag at the corner, the corner rounding can be considered first. In terms of parameters, the focus can be reduced and the air pressure can be increased; If there is hard slag hanging on the whole, it is necessary to reduce the focus, increase the air pressure and increase the cutting nozzle, but if the focus is too low or the air pressure is too high, the section will be stratified and rough; If there is granular soft slag hanging on the whole, the cutting speed can be appropriately increased or the cutting power can be reduced; If there is slag hanging on the side near the end of cutting, you can check whether the gas supply is insufficient and the gas flow can not keep up.
(2) Cutting carbon steel section: thin plate section is not bright enough and thick plate section is rough. To have a bright cross-section, first of all, the plate must be good, and the surface must be free of rust, paint and oxygen. Secondly, the oxygen purity must be as high as 99.5%. When cutting, use a small cutting nozzle with a double layer of 1.0 or 1.2. The cutting speed needs to exceed 2m / min, and the cutting air pressure should not be too high; If you want to have good quality of thick plate cutting section, you must first ensure the purity of plate and gas, and then select cutting nozzle. The larger the hole diameter, the better the section quality, but at the same time, the section taper will be larger.
Leave a Comment