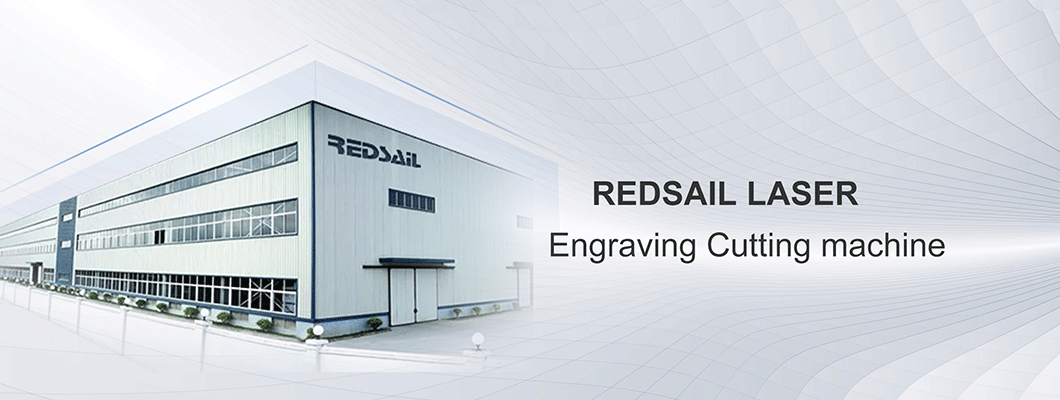
Laser cutting machine has the advantages of high cutting accuracy, high speed, no limitation of cutting pattern, low production cost, and is gradually replacing the traditional metal cutting process equipment. At present, the laser cutting machine is more and more widely used. The cutting accuracy of the laser cutting machine is related to the processing technology, which is also one of the issues that buyers are more concerned about. Many people have some misunderstandings about the understanding of laser cutting accuracy. In fact, the cutting accuracy of laser cutting machine is not mainly determined by the equipment itself, but is affected by many factors. Next, let's briefly understand what factors are likely to affect the cutting accuracy of the laser cutting machine.
A. The size of the light spot after the laser beam passes through the focus. The lower the light point of the laser beam, the higher the cutting accuracy.
B. The walking accuracy of the operating platform determines the repeated accuracy of cutting. The greater the accuracy of the operating table, the greater the cutting accuracy.
C. The greater the thickness of the workpiece, the smaller the accuracy and the larger the joint. Because the laser beam is conical, the seam is also conical, and is also stainless steel, the gap of 0,. 3mm stainless steel is much smaller than that of 2mm stainless steel.
D. Workpiece material has great influence on laser cutting accuracy. Similarly, the cutting accuracy of stainless steel is higher than that of aluminum, and the cutting surface is smoother.
Cutting speed and cutting effect of laser cutting machine
Laser cutting is free of burrs, wrinkles and high accuracy. For many mechanical and electrical manufacturing industries, the modern CNC laser cutting system controlled by computer system can easily cut workpieces of different shapes and sizes, often taking precedence over punching and die pressing processes; Although the processing speed of the laser cutting machine is still slower than that of the mold, it does not consume the mold and does not need to maintain the mold, but it also saves the time to replace the mold, and then saves the processing cost and reduces the production cost, so it is more cost-effective on the whole. In the industrial manufacturing system, many metal materials, regardless of their hardness, can be cut directly and invisibly. However, for high reflective materials such as gold, silver, copper and aluminum alloys, laser cutting is very difficult or even impossible because they are also good heat transfer conductors.
The auxiliary gas suitable for cutting materials is added in the laser cutting process. During steel cutting, oxygen, as an auxiliary gas, reacts exothermically with molten metal to form oxides, and helps blow away the slag in the cutting seam. Compressed gas, cotton, paper and other flammable materials are used to cut polypropylene and other plastics. The auxiliary gas entering the nozzle can also cool the focus lens to prevent dust from entering the lens seat, contaminating the lens and causing the lens to overheat. It is also very important to select the cutting speed of the laser cutting machine during the cutting process. The better cutting rate range can be determined according to the equipment representation or experiment. The cutting rate also changes due to the thickness of the material, the difference of the material, the melting point, the thermal conductivity and the interfacial tension after melting.
Specific performance:
A. The cutting quality can be improved by properly increasing the cutting rate, that is, the cut is slightly narrow, the cut surface is smoother, and the deformation is reduced.
B. The cutting speed is too fast to make the energy of the cutting line lower than the required value. The jet in the cutting seam cannot blow away the molten cutting solution immediately, resulting in a large amount of drag. With the hanging of the cut slag, the quality of the cut surface decreases.
C. When the cutting rate is too low, because the cutting point is a plasma arc anode, in order to maintain the stability of the electrical isolation itself, the anode spot or anode area needs to find the conduction current around the electrical isolation joint, and at the same time, transfer more heat to the jet shaft, so that the cut becomes larger, the molten materials on both sides of the cut gather at the bottom, producing slag that is not easy to clean, and the upper edge of the cut produces arc due to excessive heating and melting.
D. When the speed is very low, the electric arc will even be destroyed because of the too wide incision. It can be seen that good cutting quality cannot be separated from cutting speed.
Stability of laser cutting machine
How to measure the stability of the laser cutting machine is a problem that many buyers are more concerned about. At present, the common laser cutting machine on the market is mainly composed of main machine, slide rail, rack or ball screw, transmission mechanism and other components. Let's make a simple analysis from several parts.
The main engine is composed of a beam and two vertical end frames. The gantry of the machine is composed of an end frame and a beam. The cross beam is of rectangular square tube structure, quenched to remove internal stress, and has high strength and rigidity. Multiple mobile vehicles can be installed on the beam. Horizontal mobile equipment adopts drag chain. The mechanical part is driven by high-precision gear and rack, and the slide rail is refined by high-precision common imported guide rail. The precision machined sliding guide rail is tightened on the premise of concrete or steel frame with bracket, and equipped with adjusting bolts for installation and adjustment. The vertical drive system is installed in the vertical end frame, and the low area design makes the drive more reasonable and stable.
There are two rollers at the bottom of the vertical end frame, which can roll smoothly along the slide rail. The front end and rear end are equipped with slide rail scrapers to ensure that the surface of the slide rail is free of debris. Both sides of the bottom end are equipped with guide eccentric clamping wheels. In order to ensure the guiding accuracy of the equipment, the laser cutting machine has added a high-toughness linear guide rail (transverse drive or high-precision precision grinding slide rail) in the transverse drive and cutting torch lifting. The precision machined gear and rack ensure the longitudinal and transverse transmission accuracy of the equipment and reduce the clearance
Leave a Comment