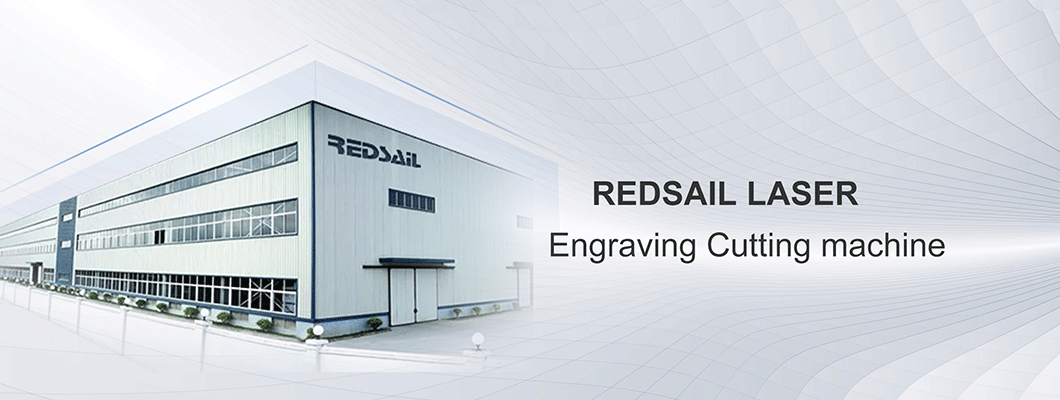
In the laser cutting process, if the focus position is different, the cutting quality will be different. In order to improve the quality of laser cutting machine, it is very important to adjust the focus position of laser cutting machine.
Nowadays, with the rapid development of economy, laser cutting machine has quietly entered people's life. With the continuous improvement of people's material level, especially the continuous improvement of technology, this is inseparable from the continuous accuracy of laser cutting and carving.
For parts with high cutting accuracy or large thickness, laser cutting machine must master and solve some key technologies. Focus position control technology is one of them. The main advantage of the laser cutting machine is that the energy density of the laser beam is high, so the diameter of the focus should be as small as possible to produce a narrow slit. As the focal depth is smaller, the focal diameter is smaller. For high-quality cutting, the effective focal depth is also related to the lens diameter and cutting material. Therefore, the position of the control focus relative to the surface of the material to be cut is very important.
Determine the focus position to make the laser cutting machine better
We analyze the cutting focus from the following three aspects: different materials and different requirements
First, the cutting focus is on the workpiece surface:
This mode, also known as zero focus, is usually used to cut SPC, SPH, SS41 and other workpieces. When in use, the focus of the tool is close to the workpiece surface. In this mode, the smoothness of the upper and lower surfaces of the workpiece is different. Generally speaking, the cutting surface near the focus is smooth, while the lower surface far away from the focus is rough. The mode shall be determined according to the process requirements of upper and lower surfaces in practical application.
Secondly, the cutting focus is on the workpiece:
This is also called positive attention. When the workpiece you need to cut is stainless steel or aluminum steel plate, you usually use the cutting point mode in the workpiece. However, one disadvantage of this method is that due to the focusing principle, the cutting amplitude is larger than the amplitude of the cutting point on the workpiece surface. At the same time, the cutting airflow required in this mode is large, the temperature is sufficient, and the cutting and piercing time is slightly longer. Therefore, when you choose the material of the workpiece, it is mainly stainless steel or aluminum lamp with high hardness.
Third, the cutting focuses on the workpiece:
In this way, since the cutting point is not located on the surface or inside of the cutting material, but above the cutting material, we also become a negative focus. This method mainly uses materials with high cutting thickness. In this way, the focus is above the cutting material, which is mainly because the thick plate needs a large cutting range, otherwise the oxygen delivered by the nozzle will easily lead to insufficient cutting temperature drop. However, one disadvantage of this method is that the cutting surface is relatively rough and it is not very practical for high-precision cutting.
Because the laser power density has a great influence on the cutting speed, the selection of lens focus is also an important issue. After the laser beam is focused, the spot size is proportional to the focal length of the lens. After focusing with a short focus lens, the spot size is very small, and the power density at the focus is very high, which is very conducive to material cutting. However, its disadvantage is that the adjustment margin of focal depth is very short, which is usually suitable for high-speed cutting of thin materials. As the focal depth of the long focus lens is wide, it is suitable for cutting thick workpieces as long as it has sufficient power density.
It is difficult for the operator of the laser cutting machine to adjust the focus, so we should know more. When the focus is at the best position, the kerf is the smallest and the efficiency is the highest. The best cutting speed of fiber laser cutting equipment can obtain the best cutting effect.
Leave a Comment