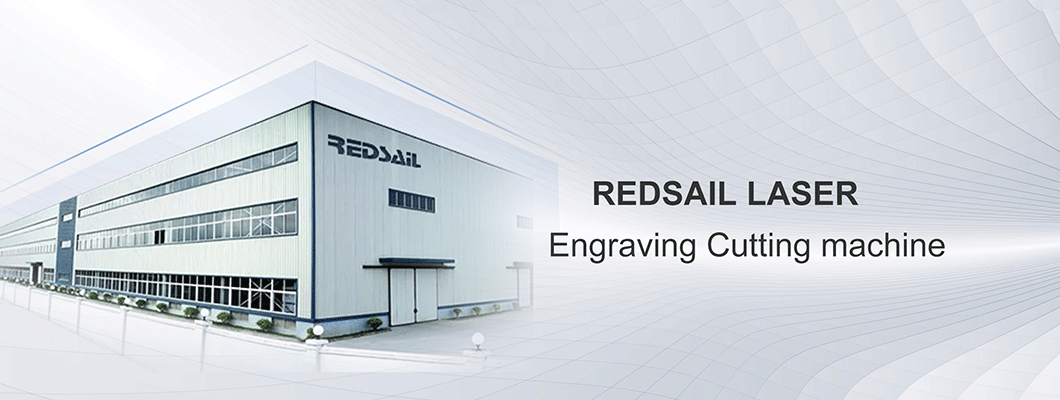
Processing capacity: both plasma cutting and laser cutting belong to thermal cutting, and plasma is more suitable for thick plates above 6mm with low accuracy requirements. However, with the development of laser cutting machines, high power laser cutting machines have emerged one after another in recent years. At present, the cutting thickness has exceeded 100mm.
Processing effect: The plasma cutting machine uses the high temperature and high heat plasma arc to melt the metal. The biggest disadvantage is that the kerf is large, the cutting end surface is rough and not smooth, and the accuracy is low. The laser cutting machine can achieve non-contact cutting, with very small kerf, high precision, small heat affected zone, smooth cutting section without burrs, and no subsequent reprocessing, saving processing and labor costs.
Use cost: products cut by laser cutting machine do not need to be processed and polished again. The later use cost and labor cost have been greatly reduced.
Plasma laser cutting machine is generally used for rough machining.
Laser cutting machines are mostly used in high-precision sheet metal processing, aerospace, intelligent equipment, engineering machinery, transportation tools, power equipment and other industries.
With the rapid development of industrialization, the requirements for the precision of metal workpiece cutting in various fields are increasing. The advantages of laser cutting machines are becoming more and more obvious, and they are also used in more industries.
Leave a Comment