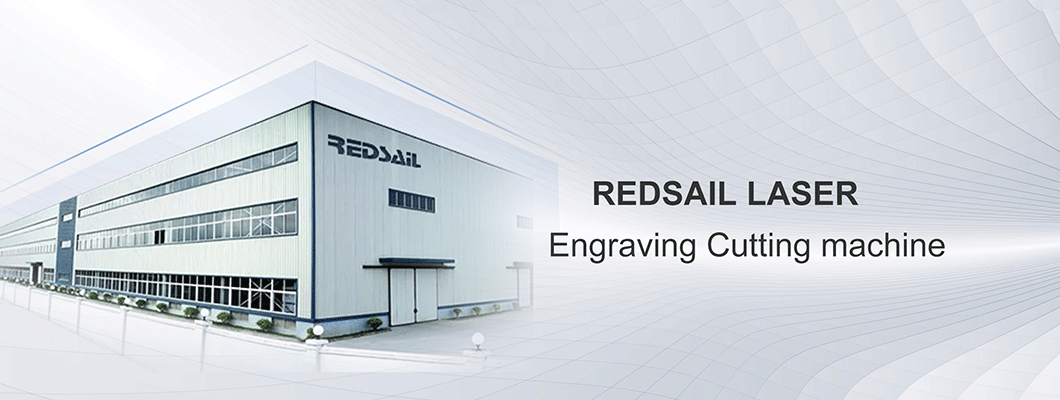
The design of the nozzle and the jet condition of the optical fiber laser cutting machine directly affect the quality of laser cutting. The manufacturing accuracy of the nozzle is closely related to the cutting quality. The main functions of the nozzle are as follows:
(1) Prevent cutting stains and other sundries from rebounding to the focus lens damaged by the cutting head.
(2) The nozzle can change the conditions of cutting gas injection, control the area and size of gas diffusion, thus affecting the cutting quality.
Relationship between nozzle and cutting quality:
When the nozzle center is different from the laser center, the impact on the cutting quality is as follows:
1) The cutting section is affected. When the cutting gas is ejected, the amount of gas is uneven, which makes one side of the cutting section easy to produce molten stains, while the other side does not appear molten stains, which has little impact on the cutting of thin plates less than 3mm. When the cutting plate exceeds 3mm, its impact is more serious, and sometimes it cannot be cut.
2) The quality of acute angle is affected. When the cutting workpiece has acute angle or small angle, it is easy to produce local over melting, while when cutting thick plates, it may not be possible to cut.
3) The perforation is unstable and the time is not easy to control. The penetration of thick plates will cause over melting. The penetration conditions are not easy to master and have little impact on the perforation of thin plates.
In a word, the concentricity of the nozzle center and the laser is one of the important factors affecting the cutting quality, especially the thicker the cutting workpiece, the greater the influence. Therefore, in order to obtain a better cutting section, it is necessary to adjust the concentricity of the nozzle center and the laser. Note: When the nozzle is deformed or there is molten spot on the nozzle, its impact on the cutting quality is the same as above. Therefore, the nozzle shall be placed carefully to avoid deformation; The molten spots on the nozzle shall be cleaned in time. In the manufacturing process, the nozzle quality has high precision requirements, and the installation method is also required to be correct. If the cutting conditions need to be changed due to poor nozzle quality, replace the nozzle in time. In the case where there is no possibility of anything between the two groups ".
Selection of nozzle diameter
The following table shows the difference in nozzle diameter.
Optical fiber laser cutting machine
The nozzle has several apertures, such as φ 1.0mm, φ 1.5mm, φ 2.0mm, φ 2.5mm, φ 3.0mm, etc. At present, nozzle diameter is usually φ 1.5mm and φ 2mm, the difference is:
1) Sheet<3mm: when used φ When 1.5mm, the cutting surface will become thinner; When using φ When it is 2mm, the cutting surface will become thicker, and there will be melting spots at the corners.
2) Thick plates above 3mm: due to the high cutting power, the relative heat dissipation time is long, and the relative cutting time is also increased. When using φ When 1.5mm, the gas diffusion area is small, which is not stable in use, but it is basically available. When using φ 2mm, the gas diffusion area is large, the gas flow is slow, and the cutting is more stable.
3) φ The diameter of 2.5mm can only be used for cutting thick plates above 10mm.
To sum up, the size of nozzle aperture has a serious impact on cutting quality and piercing quality. At present, laser cutting is commonly used φ 1.5mm and φ 2 mm bore nozzle.
The larger the nozzle aperture is, the worse the protection of the focusing mirror is. Because the sparks of the melt may come out during the cutting process, so the life of the lens will be shortened.
Leave a Comment