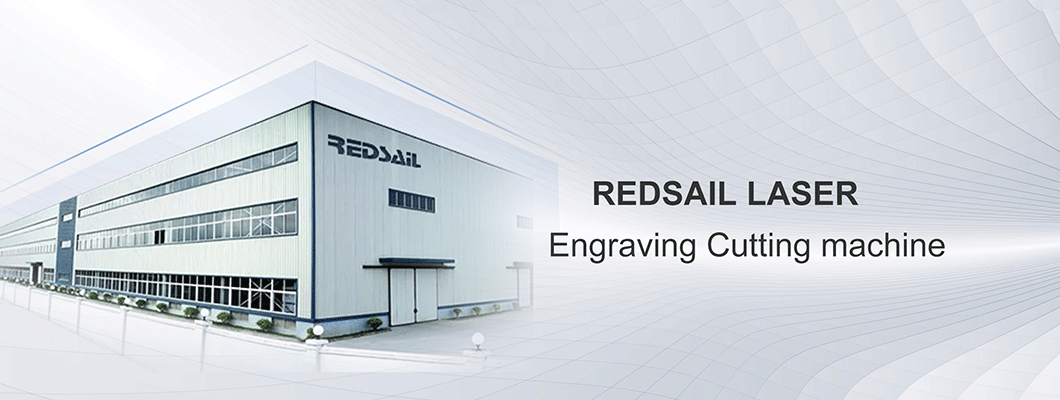
As a material cutting method, laser processing has been increasingly accepted by sheet metal manufacturers. Laser cutting has become one of the important metal processing methods in modern enterprises. Laser cutting is to use focused high power density laser beam to irradiate the workpiece, so that the irradiated material can be melted, vaporized, ablated or reach the ignition point. At the same time, high-speed air flow will blow away the molten material. Coaxial with the beam to achieve workpiece cutting.
Common problems in laser cutting of medium thick metal plates:
● Perforation of thick carbon steel plate
In the processing of thick plates, the problem of piercing time accounts for a large proportion. Various laser manufacturers have developed perforation plans. The most representative is energy perforation. The advantage of this method is that it is fast (1 second, take t16mm as an example - as shown below), but the disadvantage is that it will affect the processing of small shapes. The energy injected during the piercing process will increase the temperature of the plate and affect the subsequent overall cutting process. However, if a small power pulse is used for drilling, the time will be very long (12 seconds), resulting in reduced cutting efficiency.
● Cutting surface quality problems
When cutting medium thick plates, we often encounter the problem of cutting cross sections. The quality of this cutting product is questioned. It is also accompanied by excessive combustion and serious slagging, which cannot reflect the value of high priced laser processing machines.
● Stability of whole plate processing
In the processing of the whole steel plate, local processing defects often occur. Even if the processing machine is in good condition, sometimes this phenomenon is very random.
The following solutions to the above problems:
● Peak perforation: as the name implies, the peak pulse laser with small duty cycle is used, supplemented by non fuel spraying on the material surface to remove the accessories at the opening edge. Control the reasonable frequency of pulses during cooling and piercing.
● For carbon steel, the important factor to change the cutting area is to control the heat input to the plate and realize the combustion of laser irradiated parts. For stainless steel, the important factors of cutting cross section are the improvement of light beam and the use of gas.
● Solution for processing stability: using equal length optical path (within the processing range, the length of the light propagation path between the light source and the processing head is equal) can reduce the depth of focus change, so as to maintain the same spot and focus depth
Leave a Comment