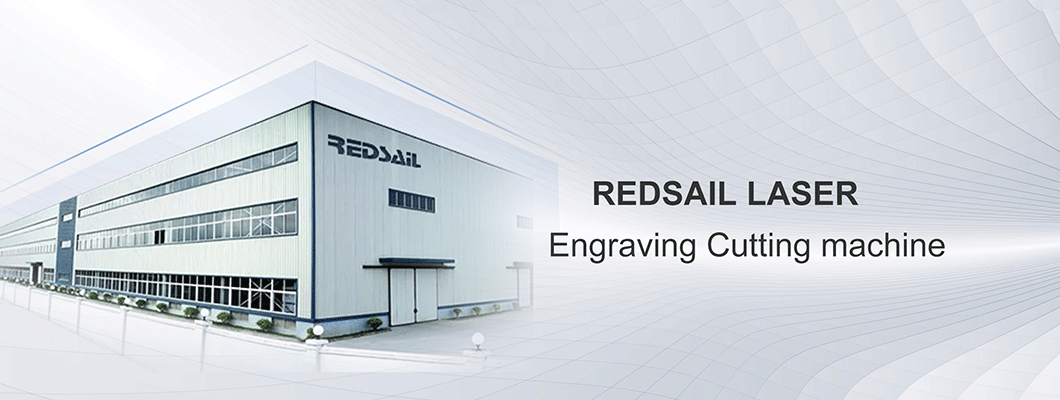
Laser cutting is one of the most common metal cutting methods, with high efficiency and convenient use, which is very common in factories. However, the use of laser cutting machines to cut metal plates will certainly produce smoke and dust. When these extremely small soot particles are produced, they will float in the air in large quantities, seriously reducing the air quality and damaging the working environment. High concentrations of smoke and dust are also extremely harmful to workers working in them, often leading to respiratory diseases and other serious diseases. How to deal with the smoke generated by the laser cutting machine? What is the best and most effective way to deal with the smoke?
At present, the commonly used laser cutting dust removal methods are mainly divided into dry and wet. The dry type is to add a set of dust collection and purification equipment for laser cutting, while the wet type is to place the cutting process on the water surface to form a water bed cutting platform, which uses the power of water flow to absorb dust and purify it. After comprehensive comparison of the two methods, the dry treatment method, especially the blowing and cutting smoke purification system, is the most popular in the factory because it is the most convenient to install and use. The smoke generated by laser cutting is concentrated below the workpiece incision, so the invention has an air inlet below the workbench, the lower part of the workbench is divided into a uniform small air suction area, and the smoke generated can be collected in the small cutting area by air suction.
One side of the cutting smoke and dust purification system platform is also provided with a sliding suction pipe, the sliding suction pipe is provided with an air inlet that can move with the cutting head, and the opposite side is also provided with an air blowing port. When soot is generated, the wind at the air blowing port will blow the soot toward the air suction port, so as to achieve the capture effect of small air volume and high soot collection rate.
The collected cutting dust will be uniformly transported to the dedusting host for filtering. The host structure is the same as the centralized dedusting system for welding dust. The installed filter cartridge will intercept more than 0.3 μ M dust to complete the cleaning process of cutting dust. The efficiency of this kind of dust removal equipment for laser cutting dust is more than 90%, and the effect is very obvious. Because of its simple installation and low cost, it has become the most popular dust removal method for laser cutting.
Leave a Comment