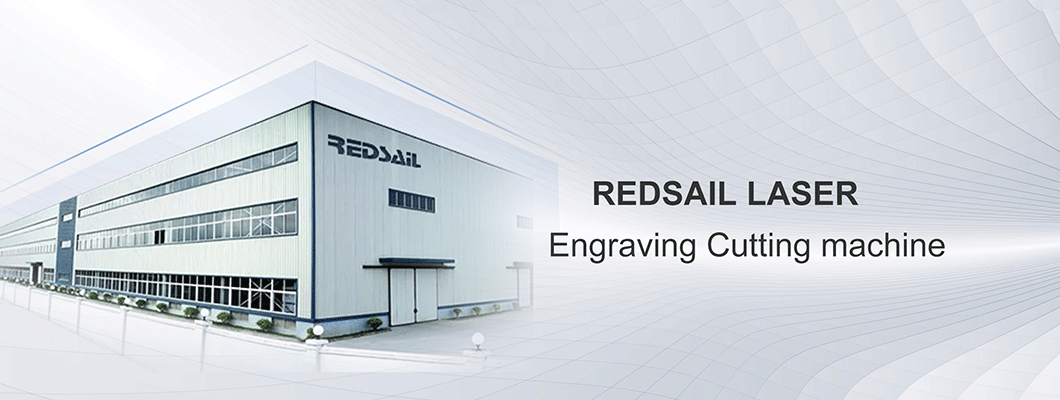
Stainless steel is a common metal material in daily life, and cutting technology is widely used when processing stainless steel raw materials. Currently, the most suitable method for cutting stainless steel is laser cutting. Laser cutting machine technology uses a high-power density laser beam to irradiate a metal surface, causing the irradiated material to melt. At the same time, high-speed gas blowing in the same direction and coaxial direction is used to remove molten substances, thus achieving the purpose of cutting workpieces.
Under normal circumstances, laser cutting of stainless steel results in higher quality metal workpieces. However, some users may encounter situations where the cutting effect is not ideal. This article analyzes the factors that affect the cutting effect of stainless steel and the solutions, hoping to provide assistance for you in operating fiber laser cutting machines.
Setting the cutting height and selecting the cutting head nozzle
When cutting stainless steel, the cutting height should be adjusted between 0.8mm-1.2mm. If the actual cutting height is not accurate, it needs to be calibrated. Select the appropriate nozzle size and model based on the thickness of stainless steel, and inspect the nozzle for damage and normal roundness before laser cutting stainless steel. Finally, adjust the cutting parameters.
Check the cleanliness of the lenses
Check if the protective lenses are clean and require no water, oil, or residue. Sometimes protective lenses may become foggy due to weather or low auxiliary gas temperatures, so it is important to clean the lenses.
Control of focal point position, cutting pressure, cutting power, and cutting speed
When laser cutting stainless steel, if there is only corner slag hanging, corner rounding can be considered first. In terms of parameters, the focus can be reduced and the air pressure can be increased.
If the entire workpiece is stuck with slag, it is necessary to reduce the focus, increase the air pressure, and increase the cutting nozzle. However, it is important to note that low focus or excessive air pressure can cause delamination and roughness of the cross-section.
If there is granular soft slag hanging on the whole, the cutting speed can be appropriately increased or the cutting power can be reduced.
If there is slag hanging on the side near the end of cutting stainless steel, it is necessary to check whether the gas supply is insufficient and the airflow cannot keep up.
The Influence of Plate Quality and Auxiliary Gas
When laser cutting stainless steel, there are problems such as insufficient brightness of the thin plate section and rough section of the thick plate.
If the thin plate section is not bright enough, first check the quality of the stainless steel plate to ensure that the surface of the metal plate is free of rust, paint, and oxide layer. Secondly, check the purity of the auxiliary gas to ensure that the oxygen purity is above 99.5%. Also note that when cutting sheet metal, it is necessary to use a small nozzle with a double layer of 1.0 or 1.2, and the cutting speed should be above 2m/min, while the cutting pressure should not be too high.
If the cutting section of a thick plate is rough, first ensure the quality of the plate and the purity of the gas. Secondly, the selection of nozzles is crucial. The larger the aperture, the better the cross-sectional quality, but at the same time, the greater the cross-sectional taper.
Compared to traditional stainless steel cutting methods, fiber laser cutting machines have simpler operations and more efficient processing. And the above precautions can effectively avoid quality issues in cutting. I believe that laser cutting machines will become increasingly popular in the selection of metal cutting processes.
Leave a Comment