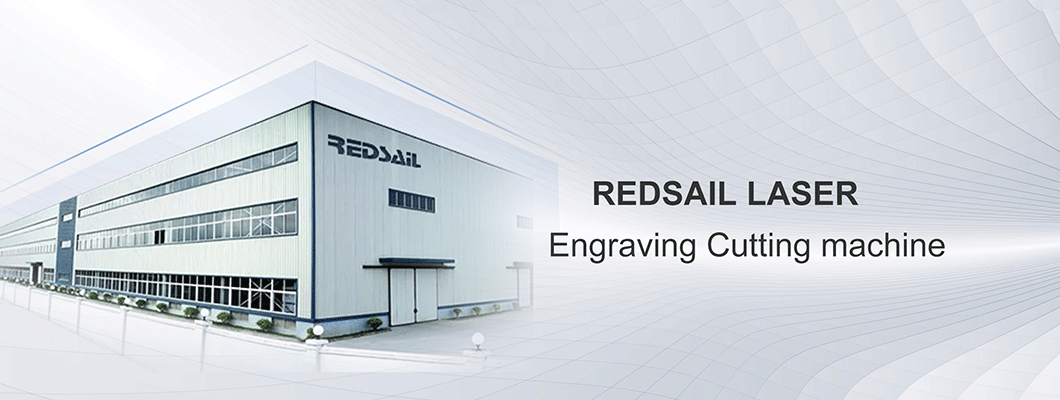
In recent years, optical fiber laser cutting machine has been widely used, and more people know its function. Friends who have used laser cutting machine know that the laser cutting effect is controlled by cutting parameters such as auxiliary air pressure, laser power, cutting speed, focus position, and so on. As for how to adjust the equipment parameters in the process of use, most people will refer to the instructions of laser cutting machine and the cutting materials in the instructions, The material thickness and cutting speed will be marked in detail.
For beginners, when they encounter poor cutting quality, they will make difficulties and do not know how to adjust many parameters. The following is a brief introduction to the problems and solutions.
Parameters affecting cutting quality include cutting height, cutting nozzle model, focus position, cutting power, cutting frequency, cutting duty ratio, cutting air pressure and cutting speed. Hardware conditions include: protective lens, gas purity, plate quality, focusing lens and collimating lens.
How to adjust the parameters of laser cutting machine?
In case of poor cutting quality, it is recommended to carry out general inspection first. The main inspection contents and sequence of general inspection are:
1. The cutting height (the actual cutting height is recommended to be between 0.8~1.2mm). If the actual cutting height is not accurate, it needs to be calibrated.
2. Check whether the cutting nozzle model and size are wrong. If it is correct, check whether the cutting nozzle is damaged.
3. It is recommended to use the cutting nozzle with diameter of 1.0 to check the optical center, and the focus is between - 1 and 1 when checking the optical center. The light point is small and easy to observe.
4. Protective lens Check whether the protective lens is clean and free of water, oil and slag. Sometimes the protective lens will be fogged due to the weather or too cold paving air.
5. Focus Check whether the focus is set correctly. If it is an autofocus cutting head, you must use the mobile phone APP to check whether the focus is correct.
6. Modify cutting parameters
After checking the above items and finding no problems, modify the parameters according to the phenomenon.
How to adjust the parameters according to the phenomenon? The following is a brief introduction to the conditions and solutions encountered when cutting stainless steel and carbon steel.
For example, there are many types of stainless steel slag. If only corner slags are hung, the corner rounding can be considered first. In terms of parameters, the focus can be reduced and the air pressure can be increased.
If hard slag is hung on the whole, it is necessary to reduce the focus, increase the air pressure and increase the cutting nozzle, but too low focus or too high air pressure will lead to section delamination and surface roughness. If granular soft slag is hung on the whole, the cutting speed can be appropriately increased or the cutting power can be reduced.
When cutting stainless steel, you may also encounter slag hanging on the side near the end of cutting. You can check whether the gas supply is insufficient and the gas flow cannot keep up.
Cutting carbon steel will generally meet the following problems: the thin plate section is not bright enough, and the thick plate section is rough.
Generally speaking, 1000W laser can cut carbon steel no more than 4mm bright, 2000W is 6mm, 3000W is 8mm.
If you want to cut the section bright, first of all, the surface of the plate must be free of rust, paint and oxide skin, and then the oxygen purity must be at least 99.5% higher. In cutting, you need to pay attention to the following: use a small cutting nozzle with double layers of 1.0 or 1.2, the cutting speed needs to exceed 2m/min, and the cutting pressure should not be too high.
If you want the quality of the thick plate cutting section to be good, you must first ensure the purity of the plate and gas, and then select the cutting nozzle. The larger the hole diameter, the better the section quality will be, but at the same time, the greater the section taper will be
Leave a Comment