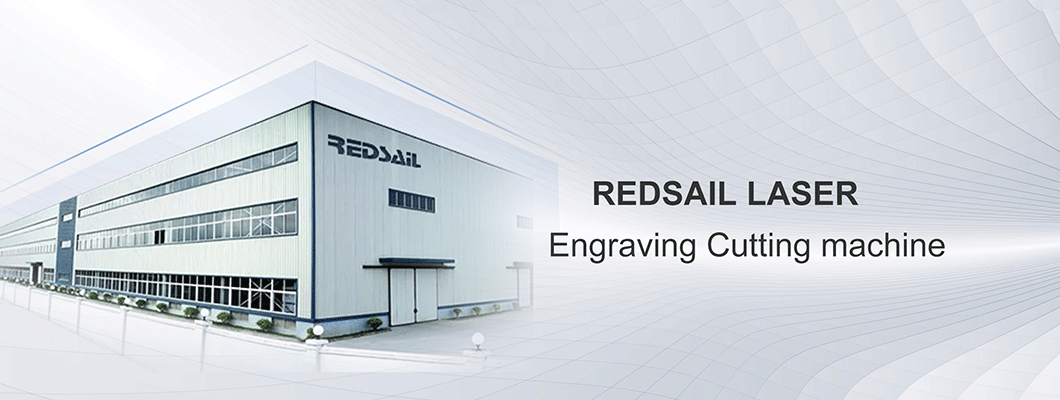
In laser cutting machine, several key technologies must be mastered. It also solves the problem of parts with high cutting accuracy or large thickness. Focus position control is one of them. One of the advantages of laser cutting is the high energy density of the beam. Therefore, the focal spot diameter should be as small as possible to form a narrow gap. Because the focal depth of the focusing lens is small, the focus diameter is small. For high-quality cutting, the effective focal depth is also related to the lens diameter and the material to be cut. Therefore, it is important to control the position of the focus relative to the surface of the cutting material.
How to cut the sample with laser cutting machine?
The laser power density has a great influence on the cutting speed. The choice of lens focal length is an important issue. After the laser beam is focused, the spot size is proportional to the focal length of the lens. After focusing with a short focus lens, the spot size is small, and the power density is high when focusing, which is conducive to material cutting. However, its disadvantage is that the focus depth is very short and the adjustment margin will be adjusted. Small size, usually suitable for high-speed cutting of thin materials. Because the telephoto lens has a wide focal depth, it is suitable for cutting thick workpieces as long as it has sufficient power density.
After determining which focal length lens to use, the relative position of the focus relative to the workpiece surface is particularly important to ensure the cutting quality. Because of the high power density at the focus, in most cases, the focus position during cutting is only on the workpiece surface or slightly lower than the surface. In the whole cutting process, ensuring the constant relative position of the focus relative to the workpiece is an important condition to obtain stable cutting quality. Sometimes, the lens is heated due to poor heat dissipation, and the focal length changes, which requires timely adjustment of the focus position.
When the focus is at an appropriate position, the gap is small, the efficiency is high, and the cutting speed can obtain good cutting effect. In most applications, the beam focus is adjusted only below the nozzle. The distance between the nozzle and the workpiece surface is usually about 1.5mm.
In the process of laser application, problems such as focusing often occur. There are three convenient methods to determine the focus position:
(1) Printing method: move the cutting head from top to bottom. In addition, laser beam printing is performed on the plastic plate, and the smaller diameter is the focus.
(2) Inclined plate method: place the plate at an angle. Pull the horizontal axis vertically to find the smaller laser beam part as the focus.
(3) Blue spark method: take down the nozzle and blow out air. Then pulse the laser on the stainless steel plate to move the cutting head. From top to bottom until the blue spark becomes larger.
Leave a Comment