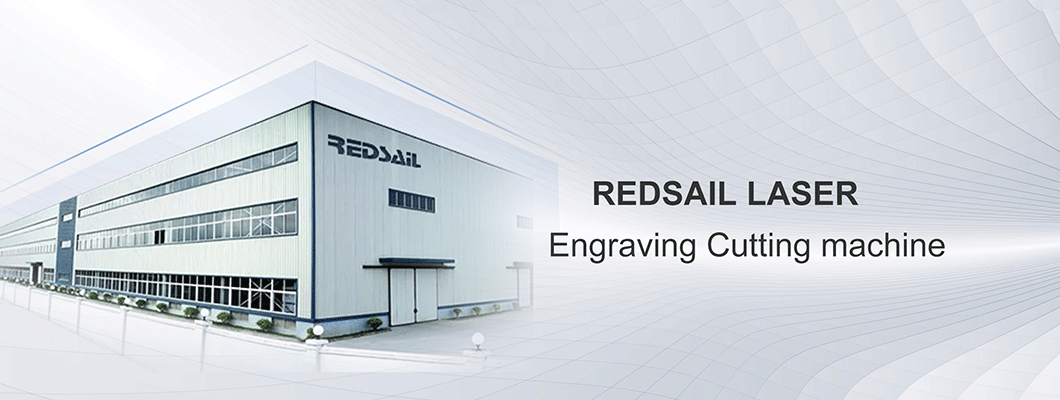
The laser cutting accuracy is an important factor to measure the quality of a fiber laser cutting machine. The four major factors that affect the accuracy of the laser cutting machine are processing size errors, which are often encountered when using the laser cutting machine for processing. This fault not only affects the production efficiency, but also increases the production cost. In fact, the accuracy of metal laser cutting machine does not depend entirely on the equipment itself, but consists of many factors.
1、 The laser agglomeration size of the laser generator: if the light spot is very small after aggregation, the cutting accuracy is very high, and if the gap after cutting is also very small. It shows that the laser cutting machine has very high accuracy and quality. But the laser beam is tapered, so the slit is also tapered. Under this condition, the greater the thickness of the workpiece, the lower the accuracy, so the larger the kerf.
2、 Precision of the workbench: If the precision of the workbench is very high, the cutting precision will also be improved. Therefore, the accuracy of the workbench is also a very important factor to measure the accuracy of the laser generator.
3、 The laser beam condenses into a cone: When cutting, the laser beam is tapered downward. If the thickness of the workpiece is very large, the cutting accuracy will be reduced, and the gap will be very large.
4、 Different cutting materials: even if the materials are the same, the cutting accuracy will be different if the components of the materials are different. Therefore, the workpiece material has a certain impact on the laser cutting accuracy.
Metal laser cutting machine is realized by using high power density energy generated after laser focusing. It uses a precision ball screw transmission mechanism and optimizes the control of the CNC system, which can meet the requirements of precision parts processing, and its dynamic performance is stable and it can work for a long time. Therefore, it has attracted much attention in metal cutting. The cutting accuracy of metal can affect the cutting process.
Since there is a problem of cutting accuracy, how can we ensure high-precision laser cutting?
Methods to improve cutting accuracy:
Focus position control technology. The smaller the focal depth of the focusing lens is, the smaller the focal spot diameter is. Therefore, it is very important to control the position of the focus relative to the surface of the material to be cut.
Cutting and piercing technology. Any kind of thermal cutting technology, except for a few cases that can start from the edge of the plate, must generally pierce a small hole in the plate. In the early days, a punch was used to punch a hole on the laser punching compound machine, and then the laser was used to cut from the small hole.
Nozzle design and air flow control technology. When laser cutting steel, oxygen and focused laser beam are shot to the material to be cut through the nozzle, thus forming an air flow beam. The basic requirements for air flow are that the air flow into the notch should be large and the speed should be high, so that enough oxidation can make the notch material fully conduct exothermic reaction; At the same time, there is enough momentum to blow out the molten material.
Laser cutting has no burr, wrinkles and high precision, superior to plasma cutting. For many mechanical and electrical manufacturing industries, because the modern laser cutting system with microcomputer program can easily cut workpieces of different shapes and sizes (the drawing of workpieces can also be modified), it is often preferred to blanking and die pressing processes; Although its processing speed is slower than that of die stamping, it has no die consumption, no need to repair the die, and saves the time to replace the die, thus saving processing costs and reducing product costs. Therefore, it is more economical on the whole. This is precisely why it is popular.
Compared with traditional plate processing methods, laser cutting has the advantages of high cutting quality (narrow incision width, small heat affected zone, smooth incision), high cutting speed, high flexibility (arbitrary shape can be cut at will), extensive material adaptability, etc.
Leave a Comment