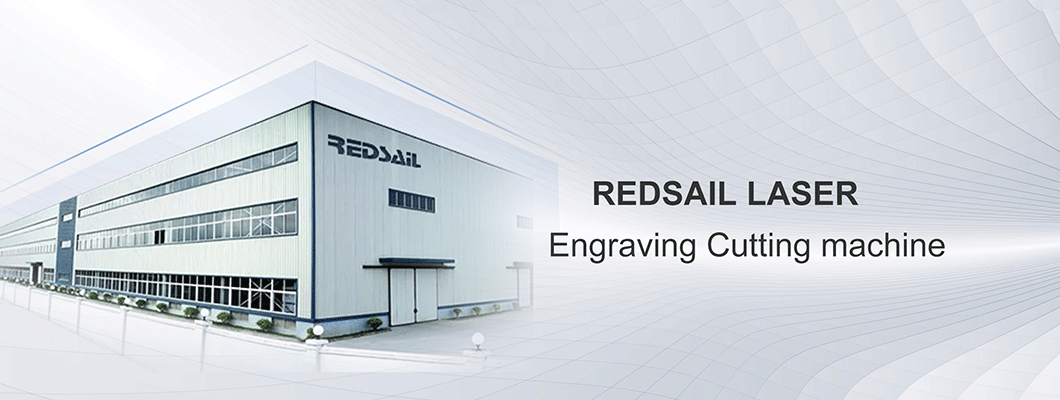
1、 Replacement of circulating water and cleaning of water tank
Ensure that the laser tube is filled with circulating water before the machine works. The quality and temperature of circulating water directly affect the service life of the laser tube. Therefore, it is necessary to replace the circulating water and clean the water tank regularly. This is best done once a week.
2、 Guide rail cleaning
As one of the core components of the equipment, guide rail and linear shaft are used to guide and support. In order to ensure high machining accuracy of the machine, its guide rails and straight lines are required to have high guiding accuracy and good motion stability. During the operation of the equipment, a large amount of corrosive dust and smoke will be generated during the processing of the machined parts. These smoke and dust will be deposited on the surface of the guide rail and the linear shaft for a long time, which has a great impact on the processing accuracy of the equipment, and will form corrosion spots on the surface of the guide rail and the linear shaft, shortening the service life of the equipment. Therefore, clean the machine guide rail every half a month. Turn off the machine before cleaning.
3、 Fan cleaning
The long-term use of the fan in the machine will accumulate a lot of solid dust in the fan, make the fan produce a lot of noise, and is not conducive to exhaust and deodorization. When the suction of the fan is insufficient and the smoke exhaust is not smooth, the fan should be cleaned.
4、 Lens cleaning
There will be some mirrors and focus mirrors on the machine. The laser light is reflected and focused by these lenses and then emitted from the laser hair.
The lens is easy to be stained with dust or other pollutants, resulting in laser loss or lens damage. So clean the lens every day.
Pay attention to:
1. The lens should be wiped gently without damaging the surface coating;
2. The wiping process should be handled with care to prevent falling;
3. Please keep the concave surface downward when installing the focus lens.
5、 Fastening of screws and couplings
After the motion system works for a period of time, the screws and couplings at the motion joints will become loose, which will affect the stability of mechanical movement. Therefore, during the operation of the machine, it is necessary to observe whether there is abnormal noise or abnormal phenomenon in the transmission parts. If problems are found, it is necessary to strengthen and maintain them in time. At the same time, the machine should use tools to tighten the screws one by one over a period of time. The first firmness should be about one month after the equipment is used.
6、 Inspection of optical path
The optical path system of the machine is completed by the reflection of the reflecting mirror and the focusing of the focusing mirror. There is no deviation of the focusing mirror in the optical path, but the three reflecting mirrors are fixed by the mechanical part, and there is a high possibility of deviation. Although usually there is no deviation, it is recommended that the user check whether the optical path is normal before each work.
Every other week, the lubrication oil filling of x-axis guide rail and lead screw, Y-axis guide rail and lead screw, z-axis guide rail and lead screw must be checked to maintain the lubrication of all moving parts and prolong the service life of X, y, z-axis guide rail and lead screw. b。 Depending on the environment of the workshop, check the contamination of the surface of the reflecting mirror and focusing mirror irregularly (at least once a month), and clean the optical lens in time to ensure its service life (see the maintenance of optical lens for details)
Regularly clean the sundries at the exhaust outlet to ensure the exhaust effect.
Regularly check the filter in the air circuit and timely remove the accumulated water and sundries in the filter.
Regularly check whether the screws of travel switch bracket and striker bracket are loose.
The dust on the filter screen of the ventilator of the electric control cabinet shall be cleaned in time to ensure good ventilation, so as to facilitate the heat dissipation of internal electrical components.
Clean the body and guide rail in time to protect the sundries in the leather cavity so as not to damage the guide rail, thus extending the service life of the guide rail.
After the machine tool is installed and used for a period of time, the level of the machine tool should be readjusted to ensure the cutting accuracy of the machine tool.
Lens cleaning
In the process of replacement, the placement, detection and installation of optical lenses shall be protected from damage and pollution. After a new lens is installed, it should be cleaned regularly.
When the laser cuts the material, a large amount of gas and splashes will be released from the working surface, which will damage the lens. When pollutants fall on the lens surface, they will absorb energy from the laser beam, resulting in thermal lens effect. If the lens has not been thermally stressed, the operator can remove it and clean it.
In the process of lens installation and cleaning, any stickiness, even nail prints or oil drops, will increase the absorption rate of the lens and reduce its service life. Therefore, the following precautions must be taken:
1. Never install the lens with bare fingers. Wear fingertips or rubber gloves.
2. Do not use sharp instruments to avoid scratching the lens surface.
3. When taking the lens, do not touch the film layer, but hold the edge of the lens.
4. The lens should be placed in a dry and tidy place for inspection and cleaning. A good workbench should have several layers of cleaning on its surface
Paper towels and several sheets of cotton paper for cleaning the lens.
5. Users should avoid speaking above the lens and keep food, beverages and other potential pollutants away from the working environment.
In the process of cleaning the lens, the method with relatively small risk should be adopted. The following operation steps are set up for this purpose and should be adopted by the user. First, use a blowing balloon to blow off the floating objects on the surface of the original, especially the lenses with small particles and flocs on the surface. This step is necessary. But never use the compressed air on the production line, because these air will contain oil mist and water droplets, which will deepen the pollution of the lens.
The second step is to slightly clean the lens with analytical pure acetone. This grade of acetone is almost anhydrous, which reduces the possibility of lens contamination.
The cotton ball dipped in acetone must be cleaned under the light and moved in a circle. Once the cotton swab is dirty, it must be replaced. The cleaning should be completed at one time to avoid the generation of wavy ribs. If the lens has two coated surfaces, such as the lens, each surface needs to be cleaned in this way. The first side needs to be placed on a layer of clean lens paper for protection.
If acetone can't remove all the dirt, then use acid and vinegar to clean. When cleaning with acid and vinegar, the dirt is removed by dissolving the dirt, but it will not cause damage to the optical lens. This acid vinegar can be of experimental grade (diluted to 50% strength), or white vinegar containing 6% acetic acid for household use. The cleaning procedure is the same as acetone cleaning, and then acetone is used to remove the acid and vinegar and dry the lens. At this time, cotton balls should be changed frequently to completely absorb the acid and hydrate. Until it is cleaned.
When pollutants and lens damage cannot be removed by cleaning, especially when the film layer is burned out due to metal spatter and dirt, the only way to restore good performance is to replace the lens.
Leave a Comment