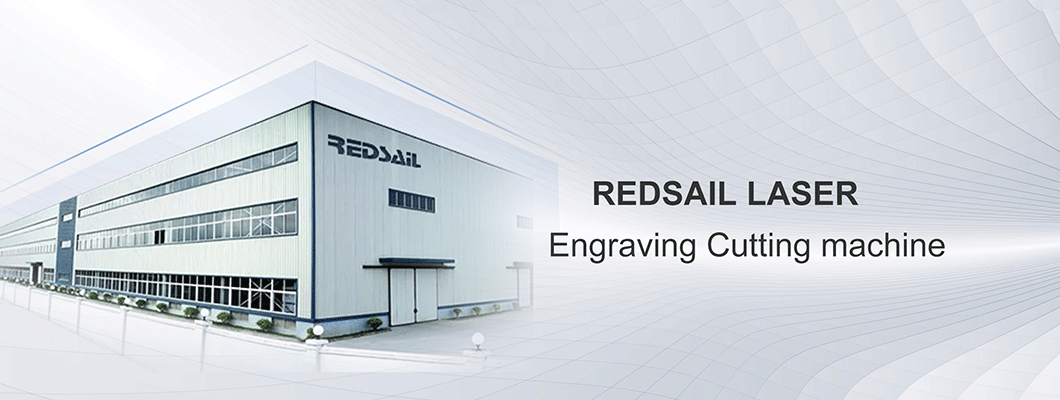
Introduction
When it comes to CO2 laser cutters, one of the essential components that play a crucial role in determining the quality of the laser beam is the mirror. Mirrors are responsible for reflecting the laser beam accurately, allowing for precision cutting and engraving. Therefore, it is of utmost importance to invest in high-quality mirrors for your CO2 laser cutter. In this article, we will discuss the key factors to consider when purchasing mirrors for CO2 laser cutters.
Optical Coating
The optical coating of a mirror greatly affects its performance. High-quality mirrors for CO2 laser cutters are typically made with special dielectric coatings that help enhance reflectivity and reduce losses. These coatings are designed to withstand the high power of the laser beam, ensuring consistent and precise reflections. It is crucial to look for mirrors with high reflectivity coatings to achieve the best results.
Materials and Durability
CO2 laser cutters operate at high power and generate a significant amount of heat. Therefore, it is essential to select mirrors made from durable materials that can withstand these conditions. The most commonly used materials for CO2 laser cutter mirrors are silicon, molybdenum, and copper. These materials have excellent thermal conductivity and are resistant to the high heat generated during laser cutting. Choosing mirrors made with such materials ensures longevity and prevents damage from excessive heat.
Surface Quality
The surface quality of a mirror plays a crucial role in determining the beam quality and, ultimately, the precision of your laser cutting and engraving. It is advisable to opt for mirrors with a high surface quality, typically classified with an optical surface specification (i.e., scratch-dig specification). Mirrors with lower quality surfaces may scatter the laser beam, leading to inaccurate cutting or engraving.
Reflectivity and Energy Loss
Another critical factor to consider when choosing mirrors for CO2 laser cutters is the reflectivity of the mirror and the energy loss it incurs. Higher reflectivity allows for more efficient laser beam transmission, resulting in better cutting and engraving quality. It is recommended to look for mirrors that offer minimum energy loss, ensuring maximum utilization of the laser energy and reducing the need for frequent replacements.
FAQs
Q: Why is mirror quality important in CO2 laser cutters?
A: Mirror quality directly affects the performance and precision of CO2 laser cutters. High-quality mirrors ensure accurate reflection of the laser beam for precise cutting and engraving.
Q: What are the ideal materials for CO2 laser cutter mirrors?
A: Silicon, molybdenum, and copper are commonly used materials for CO2 laser cutter mirrors due to their excellent thermal conductivity and heat resistance.
Q: How does surface quality impact laser cutting and engraving?
A: Mirrors with higher surface quality prevent laser beam scattering, ensuring accurate cutting and engraving results.
Q: What is the significance of reflectivity and energy loss in mirrors for CO2 laser cutters?
A: Higher reflectivity and lower energy loss enhance laser beam transmission, improving cutting and engraving quality while reducing the need for frequent mirror replacements.
Conclusion
Investing in high-quality mirrors for CO2 laser cutters is essential for achieving optimal cutting and engraving results. Considering factors such as optical coating, materials and durability, surface quality, and reflectivity will help you choose the best mirror for your specific needs. By selecting mirrors with superior performance, you can ensure precision and efficiency in your CO2 laser cutting operations.
Leave a Comment