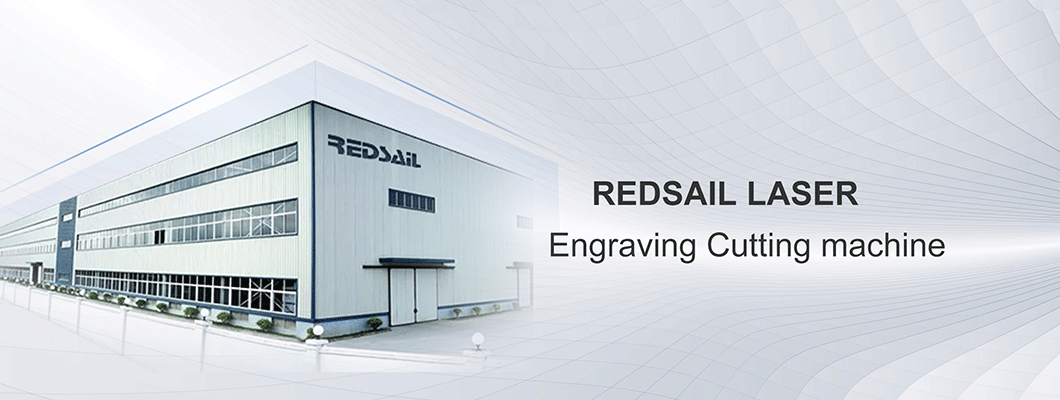
Recently, many places in the north have welcomed snowflakes. Even Guangdong, a poor household in winter, has successfully received cold air. In order to better cope with the coming cold weather and successfully complete the production plan at the end of the year, laser antifreeze measures must be taken~
The operating temperature of the laser requires that the operating environment temperature of the laser should be controlled at about 22 degrees, the low temperature water temperature of the water cooler should be set at 20-24 degrees, and the high temperature water temperature should be set at 28-30 degrees. Before the laser is light emitting, the water cooler needs to work for more than 20 minutes to ensure that the actual temperature of the water cooler reaches the set temperature, open the monitoring software, and confirm that the temperature of the laser main control board and the optical sensor of the module is above 18 degrees. If the set temperature is not reached, the monitoring interface will pop up an alarm page to prohibit light. To resume work, restart the laser and observe that the monitoring interface temperature reaches 18 degrees before lighting.
Laser light output warning
【1】 Basic principle of antifreeze
There is a "freezing point" in the cooling water. When the temperature of the cooling water is lower than the "freezing point", the volume expansion of the cooling water during solidification will cause the overflow components in the laser cooling system, such as the cold water plate, the water separator, etc., to expand, deform and crack, and the optical components to be damaged, which will cause the laser to return to the factory for maintenance. Therefore, the winter antifreeze protection measures for the laser must be taken to ensure the normal operation of the equipment.
【2】 Anti freezing solution
1 - Keep the chiller running
Under the condition that there is no power failure in the local area, the chiller can be kept running, and the low temperature water and normal temperature water can be set at about 5 ℃ (ensure that the cooling water is higher than the freezing point, and save electricity).
2 - Drain the cooling water in the machine
Drain the cooling water in the laser and water cooler after each use.
Drainage method:
Remove the water pipe at the water inlet from the chiller, and then ventilate the water inlet (WATER IN) with compressed gas until the residual water in the chiller is blown out.
Remove the water pipe at the water inlet from the laser, and then ventilate the water inlet (WATER IN) with compressed gas until the residual water in the water-cooled pipe inside the laser is blown out of the water outlet.
Remove the water pipe at the water inlet from the laser, and then ventilate the water inlet (WATER IN) with compressed gas until the residual water in the water-cooled pipe inside the laser is blown out of the water outlet. Then plug the water inlet and outlet with water pipe (or rubber plug) to prevent dust from entering the water pipe.
3 - Replace cooling water with antifreeze
When the operating environment is frequently powered off and the cooling water cannot be drained every day, antifreeze must be used.
【3】 Selection of antifreeze
1 - Please select the antifreeze with proper freezing point according to the local temperature. The choice of antifreeze is not that the lower the freezing point is, the better, but that of antifreeze slightly lower than the local temperature according to the local minimum temperature.
2-MAX laser recommends that the antifreeze for water cooler is the brand of Clariant.
Note: Any antifreeze cannot completely replace deionized water, and it is not recommended to use it for a long time all year round. Never confuse laser cutting machine antifreeze with automobile antifreeze! Lose hundreds of thousands at random
After winter, it is recommended to use deionized water or distilled water to clean the pipeline and resume using deionized water or distilled water as coolant. If the machine is shut down for a long time (such as during the Spring Festival shutdown) or before the laser is transported, the cooling water in the equipment must be drained, and compressed air must be used to blow the residual water in the equipment (including the laser and the chiller) to prevent the internal icing from damaging the components.
Leave a Comment