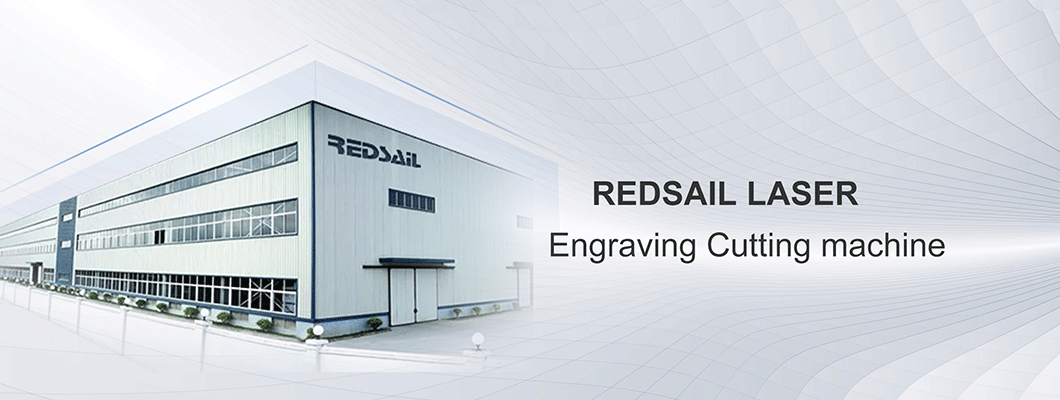
Metal and alloy materials are widely used materials, and their processing techniques are involved in all walks of life. Common metal material processing techniques include: turning, milling, planing, grinding, pliers, cutting, CNC machining, heat treatment, forging, casting, EDM, stamping, die casting, etc. According to different application scenarios, choose different processing methods. In recent years, with the advancement of science and technology, products have gradually developed in the direction of technology, integration and intelligence, which also makes new requirements for metal processing. Especially in the cutting of metal, the cutting precision is required to be higher and the effect is better.
In order to seek breakthroughs in metal cutting technology, laser micromachining technology has been gradually applied, and it has become the mainstream technology for precision cutting and drilling of metal materials. Precision laser drilling machine, also known as metal laser drilling machine, is a laser cutting equipment that can cut metal alloy materials with high precision. Using high-energy pulsed laser heat energy for thermal cutting and drilling of metal materials, the metal can reach 0.02mm, and it is suitable for micro-processing of various metals, such as punching holes for mobile phone receivers in the electronics industry, and needle tube cutting and punching in the medical industry. Compared with the traditional mechanical drilling process, electric spark discharge and electrochemistry and other drilling methods, the laser drilling accuracy can reach the micron level, which has significant technical advantages.
What are the advantages of metal laser drilling machine?
1. Fast punching speed, high efficiency; high precision, accurate positioning without deviation;
2. The edge of the aperture is smooth and flat, without burrs;
3. The heat-affected area is small, and the workpiece is not deformed or damaged. It is suitable for the drilling process of various materials such as brittle, hard and soft.
4. It is suitable for batch processing of high density and large number of holes;
5. No extra consumables are needed during use, and there is no tool loss;
6. It can punch holes on irregular and difficult-to-machine inclined and curved surfaces;
Leave a Comment