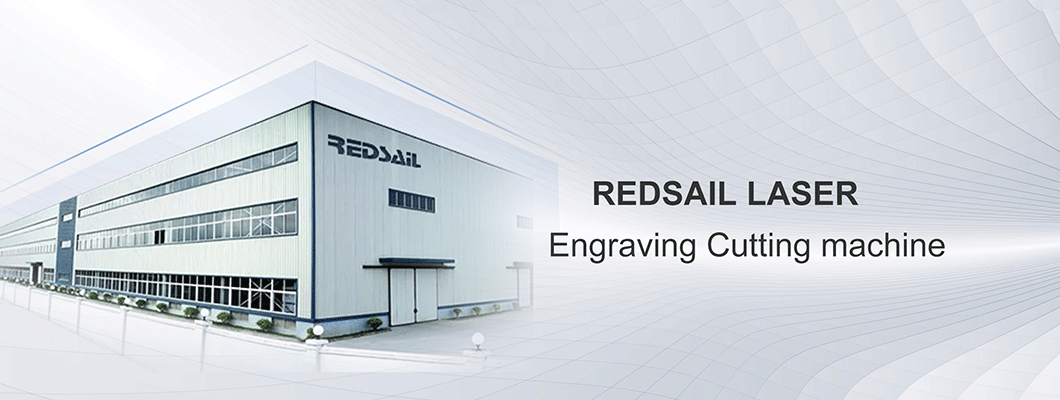
With the rapid development of laser cutting technology, laser cutting machine plays a unique role in all walks of life due to its unique advantages. The laser cutting machine has different characteristics for cutting various materials in the mechanical industry, and it also has different precautions when using the laser cutting machine to treat different materials. At present, the metal materials that need to be processed by laser cutting machine mainly include the following:
1. Carbon steel plate
The material will get good results when it is cut with oxygen. When oxygen is used as the processing gas, the cutting edge will be slightly oxidized. Modern laser cutting machines can cut carbon steel plates up to 20MM in thickness. The cutting seam of carbon steel can be controlled within a satisfactory width range by using oxidation melting cutting mechanism, and the cutting seam of thin plates can be narrowed to about 0.1MM.
2. Stainless steel
Laser cutting is an effective processing tool for the manufacturing industry using stainless steel sheet as the main component. Cutting stainless steel requires: use high-pressure nitrogen to obtain edges without oxidation and burr, so no further treatment is required. Coating oil film on the surface of the plate will obtain better perforation effect without reducing the processing quality.
3. Aluminum
Aluminum cutting belongs to the melting laser cutting mechanism. The auxiliary gas used is mainly used to blow away the molten products from the cutting area, and generally can obtain better section quality. For some aluminum alloys, attention should be paid to preventing microcracks on the surface of the slit. Pure aluminum is very difficult to cut because of its high purity. It can only be cut when the "reflection absorption" device is installed on the fiber laser cutting machine system. Otherwise, the reflection will destroy the optical components.
4. Titanium and alloy
Pure titanium can well couple and focus the heat energy converted by the laser beam. When oxygen is used as the auxiliary gas, the chemical reaction is fierce and the cutting speed is fast. However, it is easy to generate oxide layer at the cutting edge, and it will cause excessive burning if you are not careful. To be safe, it is better to use air as auxiliary gas to ensure cutting quality.
5. Copper and brass
Both materials have high reflectivity and excellent thermal conductivity. Pure copper (red copper) cannot be cut by CO2 laser beam because of its high reflectivity. Brass (copper alloy) uses high laser power and auxiliary gas uses air or oxygen, which can cut thin plates. Brass with thickness less than 1mm can be cut with nitrogen; Copper with thickness less than 2mm can be cut, and oxygen must be used for processing gas.
Leave a Comment