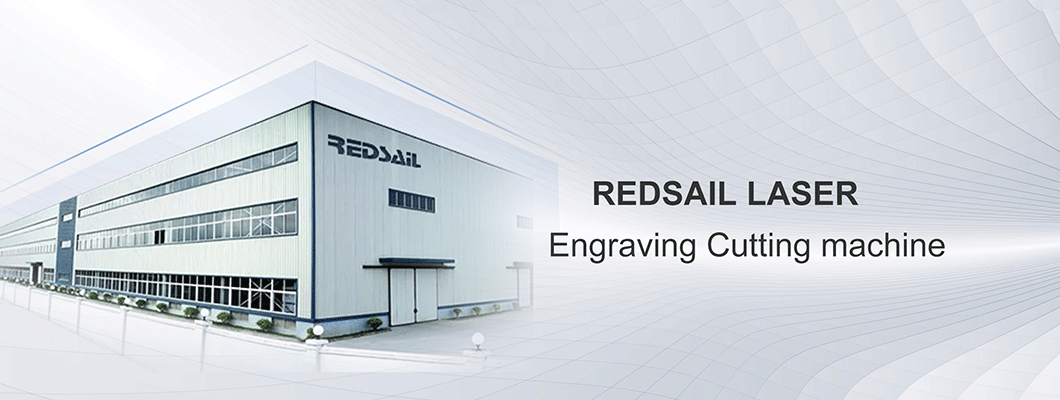
1: Influence of cutting speed on incision
1. If the cutting speed is too fast, the following consequences may be caused
It may not be able to cut through, and sparks may be scattered
Some areas can be cut through, but some areas cannot be cut through
The whole section is thick
The cutting section has oblique stripes, and the lower half is soluble
2. The speed is too slow
Resulting in over melting and rough cutting surface
The cutting seam is widened, and the sharp corner is completely melted
Affect cutting efficiency
2: Influence of auxiliary gas on cutting quality
(the gas is helpful to heat dissipation and combustion, blow away the solution stains, and improve the quality of the cutting surface)
1. Influence on cutting when gas pressure is insufficient
Melting stains on the cutting surface
Cutting speed cannot be increased, affecting efficiency
2. Influence on cutting quality when gas pressure is too high
When the air flow is too large, the cutting surface is thicker and the seam is wider
When the air flow is too large, the cut-off part will melt (burn angle), and good cutting quality cannot be formed
3: Influence of auxiliary gas on perforation
1. Influence on cutting quality when gas pressure is too low
When the gas pressure is too low, it is difficult to penetrate and the time increases
2. Influence on cutting quality when gas pressure is too high
When the gas pressure is too high, the penetration point will melt, forming a large melting point. Therefore, the pressure of thin plate piercing is higher, while that of thick plate is lower
4: The laser power has a decisive influence on the cutting process and quality
The power is too low to cut
Excessive power, melting of the whole cutting surface
Insufficient power, resulting in molten stains after cutting
Skill: when cutting carbon steel with oxygen, the skill of stably cutting small round holes!
When cutting carbon steel workpieces, it is often encountered that circular holes smaller than the thickness of the plate are cut. When cutting a small round hole, the cutting speed cannot be loaded to the normal speed when cutting a straight line. Therefore, the re debugging of cutting a small round hole should be conducted separately from the normal cutting parameters.
Cutting round holes smaller than the thickness of the plate is debugged separately from the normal round hole parameters, and different layers are used;
Use pre piercing to prevent small round hole from being burnt and melted (it is recommended to use pre piercing for carbon steel above 6mm);
Arc transition is used at the lead corner to prevent the plate from absorbing too much heat and causing corner burn; Use "real time power adjustment" according to the speed to automatically adjust the cutting power according to the real-time speed when cutting small round holes.
Leave a Comment