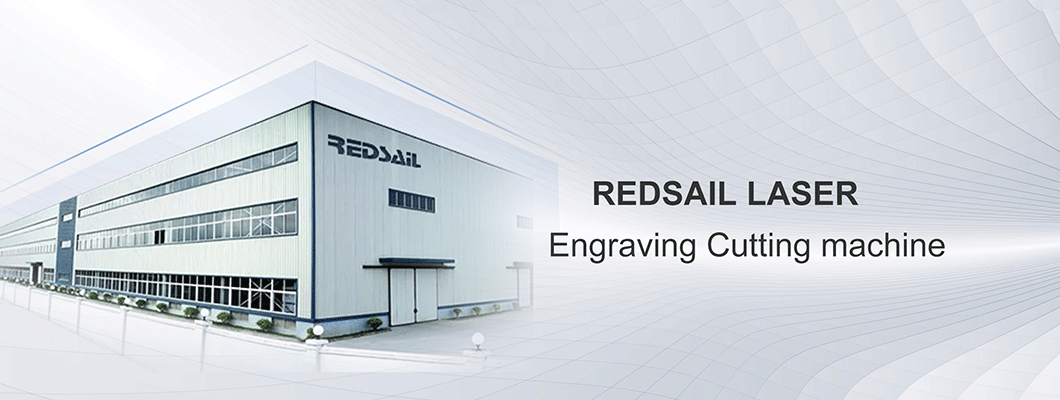
Many people are buying laser cutting machines or second-hand laser cutting machines, and do not know how to judge the quality of laser cutting machines. Generally, the quality and performance of a laser cutting machine are determined directly by the product effect of cutting. In fact, this is not scientific, because laser cutting will change in cutting speed, cutting effect and cutting power depending on the corresponding material. For laser cutting processing, Xiaobian's idea is to evaluate its processing quality mainly through the following principles:
1. The cutting surface is smooth, without stripes, burrs and brittle fracture;
When the metal laser cutting machine cuts thick plates at high speed, the molten metal will not appear in the cut at the bottom of the laser beam, but it will be sprayed by the laser beam. The result is that the curve formed on the cutting edge closely follows the moving laser beam. In order to solve this problem, we have to reduce the speed at the end of the cutting process, thus greatly eliminating the generation of wrinkles.
2. Size of cutting gap;
The slit width is narrow, which is mainly related to the size of the laser beam spot diameter. In general, the slit width of metal laser cutting machine does not affect the cutting quality. The slit width has an important impact, forming a part of a particularly accurate configuration file. This is because the cutting width determines the interior of the smallest contour. When the thickness of the plate increases, the cutting width will increase. Therefore, in order to ensure the same high accuracy, no matter how wide the cutting width is, the workpiece should be constant in the processing area of the laser cutting machine.
3. Good perpendicularity of cutting seam and small heat affected zone;
In general, the section perpendicularity of the material below 5MM cut by the metal laser cutting machine may not be the main evaluation factor, but for high-power laser cutting, when the thickness of the processed material exceeds 10mm, the perpendicularity of the cutting edge will become very important. Because the laser beam becomes divergent when it is away from the focus, the cutting becomes wider towards the top or bottom according to the position of the focus. The cutting edge deviates several millimeters from the vertical line. The more vertical the edge is, the higher the cutting quality is; The IPG laser used by the Jiatai laser cutting machine and the laser beam emitted by the machine tool are very stable, and the upper and lower errors of the 10mm products can be controlled within 0.3mm.
4. No material combustion, no molten layer formation, no large slag;
The slagging of metal laser numerical control cutting machine is mainly reflected in the deposition and section burr. This material is deposited on the surface of the workpiece as a special oil that begins to melt before the result of laser cutting. Gasified and various, the material does not need to be blown away by the customer. However, the upward or downward discharge will also form deposition on the surface. The formation of burr is one of the important factors that affect the quality of laser cutting. Because additional work is required to eliminate the burr, the severity and quantity of burr can be determined intuitively.
5. Heat effect of cutting material
As an application equipment of thermal cutting processing, metal laser cutting machine is bound to cause thermal impact on metal materials during use, which mainly includes three aspects: 1. thermal impact area; 2. Depression and corrosion; 3. Material deformation
The heat-affected area refers to the area near the incision heated during laser cutting. At the same time, the structure of the metal changes. For example, some metals will harden. The heat affected area refers to the depth of the area where the internal structure changes; And the depression and corrosion are
The surface of the edge has adverse effects on the appearance. They appear in the cutting error that should be avoided in general; If the cutting causes sharp heating of the part, it will deform. This is particularly important in fine machining, because the contour and connecting piece here are usually only a few tenths of a millimeter wide. Control of laser power and use of short laser pulses can reduce the heating of parts and avoid deformation.
6. The surface roughness of the cut is the key to measure the surface quality of laser cutting.
In fact, for the metal laser cutting machine, the cutting section grain and roughness are directly related, and often the poor cutting performance of the section grain will directly lead to higher roughness. However, considering the different causes of the two different effects, we generally analyze the metal excitation
The processing quality of CNC cutting machine is still analyzed separately. The laser cutting section will form vertical lines. The depth of the lines determines the roughness of the cutting surface. The shallower the lines, the smoother the cutting section. Roughness not only affects the appearance of the edge, but also affects the friction characteristics. In most cases, it is necessary to reduce the roughness, so the shallower the grain, the higher the cutting quality.
In addition to the above six principles, the state and shape of the molten layer during laser cutting directly affect the above processing quality evaluation indicators.
The surface roughness of laser cutting mainly depends on the following three aspects:
① Adjustable process parameters in the cutting process, such as power, cutting speed, auxiliary gas type and pressure;
② The intrinsic parameters of the cutting system, such as spot mode, focal length, etc;
③ The physical parameters of the processed material, such as the laser absorption, melting point, viscosity coefficient of molten metal oxide, surface tension of metal oxide, etc.
In addition, the thickness of machined parts also has a great impact on the surface quality of laser cutting. Relatively speaking, the smaller the thickness of the metal workpiece, the higher the roughness grade of the cutting surface.
Leave a Comment