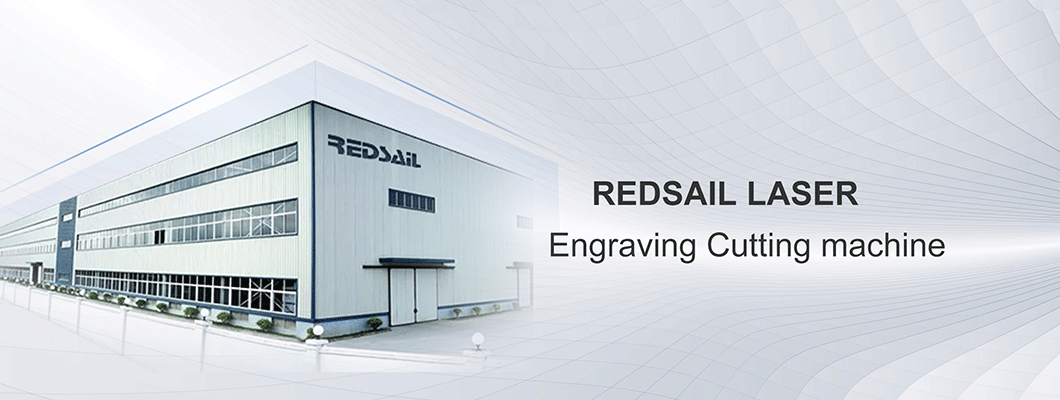
With the irreplaceable advantages of large cutting format, fast cutting speed and cutting thicker plates, high-power laser cutting machine has been widely recognized by the market once it is listed. However, as the high power laser cutting technology is still in the primary stage of popularization, although the staff of the laser cutting machine manufacturer has systematically trained the enterprise operators when delivering the equipment and training, some operators are still unskilled in the high power laser cutting skills.
Therefore, according to the summary of the technical engineers and the common problems of customers, Redsail laser summarized the following solutions to the problem of high power laser cutting technology.
When poor cutting effect is found, first check whether the following conditions occur:
1. All lenses in the laser head are clean and free of contamination;
2. The water temperature in the water tank is normal, and the laser has no condensation;
3. The cutting gas has excellent purity, smooth gas path and no air leakage.
Problem 1: Cutting with stripes
Factors causing the problem:
1. Wrong nozzle type selection and too large nozzle;
2. The air pressure is not set correctly, and excessive air pressure will cause excessive burning and streaking;
3. If the cutting speed is not correct, too slow or too fast cutting speed will also cause full overburn.
terms of settlement:
1. Replace the nozzle, replace the nozzle with a small diameter, such as 16mm carbon steel bright cutting, and choose high-speed nozzle D1.4; High speed nozzle D1.6 can be selected for 20mm carbon steel bright surface;
2. Reduce cutting air pressure and improve end face cutting quality;
3. Adjust the cutting speed, and the power should match the cutting speed appropriately,
Problem 2: There is slag at the bottom
Factors causing the problem:
1. The nozzle is too small, and the cutting focus does not match;
2. The air pressure is too small or too large, and the cutting speed is too fast;
3. The plate material is poor, the plate quality is poor, and it is difficult to remove the slag with small nozzles.
terms of settlement:
1. Replace the large diameter nozzle and adjust the focusing point to the proper position;
2. Increase or decrease the air pressure until the air flow is appropriate;
3. Select good plates.
Problem 3: Burrs on the bottom
Factors causing the problem:
1. The nozzle diameter is too small to meet the processing requirements;
2. Negative defocusing does not match, so negative defocusing should be increased and appropriate position should be adjusted;
3. The air pressure is too small, resulting in burr at the bottom and insufficient cutting.
terms of settlement:
1. Large diameter nozzle can increase air flow;
2. Increase negative defocusing to make the cutting section reach the bottom position;
3. Increasing the air pressure can reduce the burr at the bottom.
Leave a Comment