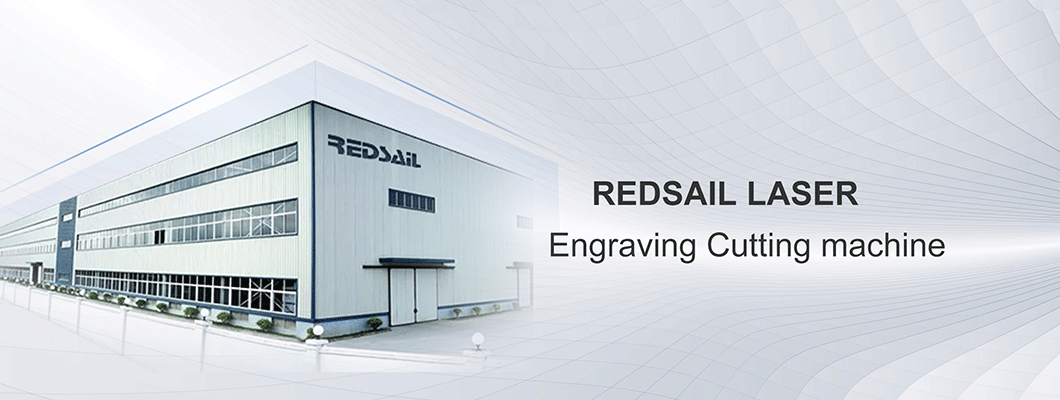
(1) The laser with small divergence angle (0.001~0.003rad) is selected for controlling the aperture size of the laser cutting machine. A small aperture can be obtained by shortening the focal length or decreasing the output energy. About high melting point. The data with good thermal conductivity can realize the machining of small holes with an aperture of 0.01~1mm, and the small aperture can reach 0.001 mm.
(2) The depth control of the laser cutting machine hole improves the laser output energy. Select a reasonable pulse width (the shorter the pulse width should be used if the data and thermal conductivity are better), and use the basic mode form (single mode with Gaussian distribution of light intensity) to obtain a large hole depth. For the deep hole with small aperture, it is better to use laser to irradiate repeatedly, and use the objective lens with short focal length (15-30mm) to drill the hole.
(3) To improve the roundness of the holes processed by the laser cutting machine, the basic mode processing is selected as the laser form, the spherical aberration free objective lens is used as the focusing lens, and the optical axis of the lens coincides with the optical axis of the laser beam. The processing roundness can be improved by properly deviating the workpiece from the focusing point and selecting the appropriate laser energy.
(4) The taper of the hole is usually increased with the aperture ratio. The taper of the hole can be reduced by selecting appropriate laser output energy or small energy for repeated irradiation, short focal length, small lens refractive index and reducing the angle between the incident light and the optical axis.
Leave a Comment