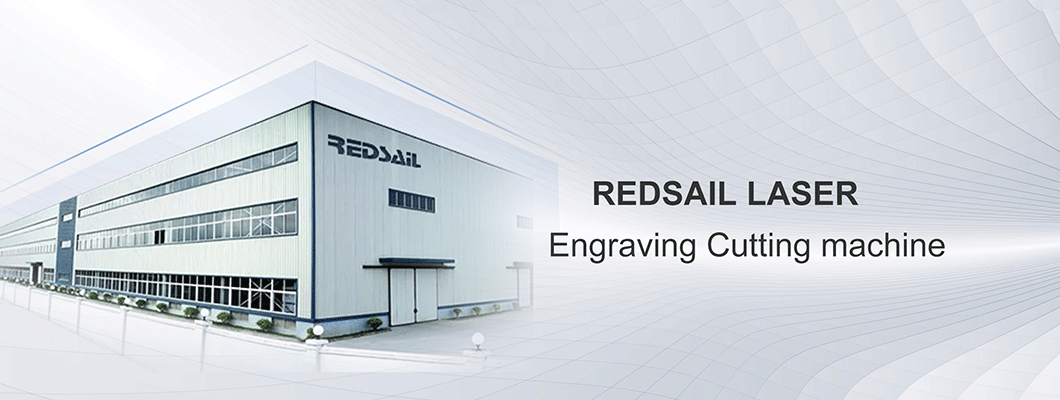
With the development of laser cutting technology in recent years, it has been widely used in more and more fields.
Laser cutting technology is widely used in the processing of metal and non-metallic materials, greatly reducing processing time, reducing processing costs, and improving the quality of the workpiece. Pulse laser is applicable to metal materials, and continuous laser is applicable to non-metallic materials, the latter is an important application field of laser cutting technology. The modern laser has become the "sword" of "cutting iron like mud" that people dream of pursuing
Laser cutting is to focus the CO2 laser beam on the material surface with a focusing mirror to melt the material, at the same time, use compressed gas coaxial with the laser beam to blow away the melted material, and make the laser beam and the material move relative to each other along the track, thus forming a shaped slit. Since the 1970s, with the continuous improvement and development of CO2 laser and numerical control technology, it has become an advanced processing method of plate cutting in industry. In the 1950s and 1960s, it was used as the main method for cutting plates: oxyacetylene flame cutting was used for medium and thick plates; Shearing machine is used for sheet metal blanking, stamping is used for forming complex parts in large quantities, and vibration shear is used for single parts. After the 1970s, in order to improve the cutting quality of flame cutting, oxyethane precision flame cutting and plasma cutting were also promoted. In order to reduce the manufacturing cycle of large stamping dies, CNC step punching and electric machining technologies have been developed. All kinds of cutting and blanking methods have their advantages and disadvantages, and are applicable in industrial production.
Leave a Comment