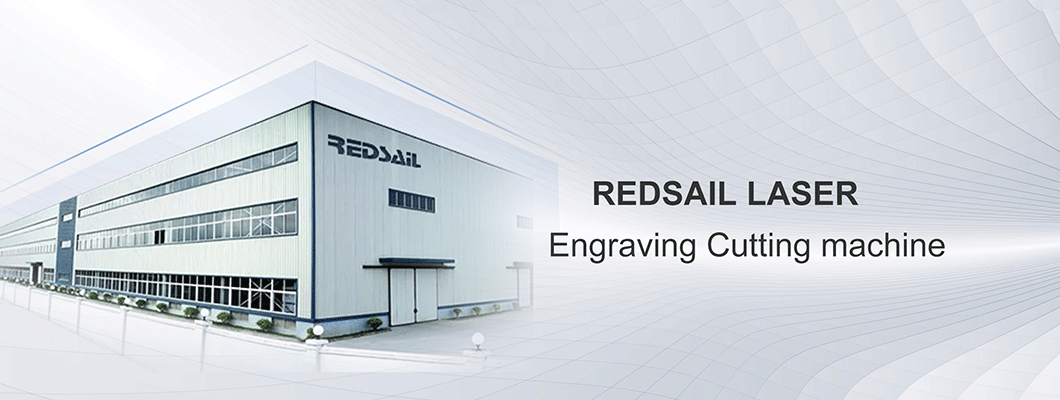
Burr is one of the common phenomena in laser cutting machine processing, and it is also the two unsolved problems "generation and control of burr" in the research of metal cutting theory so far. Burr directly affects the dimensional accuracy, shape and position accuracy and surface roughness of the workpiece to be processed. Today, I will talk about the common causes and solutions of burrs in laser cutting.
Cause 1: The laser cutting machine produces a deviation in the upper and lower positions of the laser beam focus, which leads to the energy not converging on the workpiece exactly, and the workpiece is not fully vaporized, which increases the amount of molten slag and is not easy to blow off, thus making it easier to produce burrs.
Solution: Adjust the position of the laser beam focus to the best state according to the offset position.
The second reason is that the output power of the laser cutting machine is not enough to effectively vaporize the metal, resulting in excessive slag and burrs.
Solution: check whether the laser cutting machine works normally. If not, repair and maintain it in time; If it is normal, check whether the output value is correct.
Cause 3: The cutting line speed of the laser cutting machine is too slow, which damages the surface quality of the cutting surface and produces burrs.
Solution: timely adjust and improve the cutting line speed to make it reach the normal value.
Cause 4: The purity of auxiliary gas of laser cutting machine can not meet the required standard, and it will also cause burrs on the workpiece.
Solution: replace the auxiliary gas with higher purity.
Cause 5: The laser cutting machine works for a long time, which makes the equipment unstable, which will also lead to burr.
Solution: Turn off the laser cutting machine and restart it after a period of time, so that it can have a full rest.
Leave a Comment