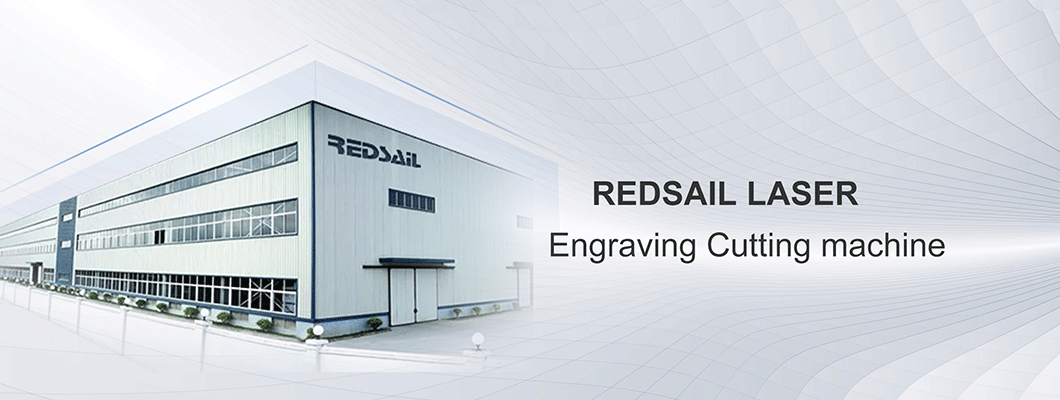
Traditional cutting process means include flame cutting, plasma cutting, water jet cutting, wire cutting and punch machining, etc. Laser cutting, as a new technology means in recent years, is to irradiate a laser beam with high energy density on the workpiece to be processed, so that the part is heated and melted, and then use high-pressure gas to blow off the slag to form a cutting seam.
Laser cutting machine has the following advantages:
1. The slit is narrow, with high precision and good slit roughness. There is no need to reprocess the next process after cutting.
2. The laser processing system itself is a computer system, which can be conveniently arranged and modified, and is suitable for personalized processing. Especially for some sheet metal parts with complex contour and shape, there are many batches and small batches, and the product life cycle is not long. From the perspective of technology, economic cost and time, it is not cost-effective to manufacture molds, and laser cutting is particularly advantageous.
3. Laser processing has high energy density, short action time, small heat-affected zone, small thermal deformation, and small thermal stress. In addition, laser processing is non-mechanical contact processing, which has no mechanical stress effect on the workpiece, and is suitable for precision processing.
4. The high energy density of laser is enough to melt any metal, especially suitable for processing some high hardness, high brittleness and high melting point
Materials that are difficult to be processed by other technological means.
5. The processing cost is low. The one-time investment of equipment is relatively expensive, but the continuous and massive processing reduces the processing cost of each part.
6. The laser is non-contact processing, with small inertia and fast processing speed. With the CAD/CAM software programming of the numerical control system, it is time-saving and convenient, and the overall efficiency is very high.
7. The laser has a high degree of automation, can be completely closed processing, low noise, and greatly improve the working environment of operators.
Fiber laser cutting machine VS early laser cutting
1. The laser is transmitted to the focusing head through optical fiber, and the flexible connection mode is easy to be matched with the production line to realize automatic work.
2. The ideal beam quality of optical fiber greatly improves the cutting quality and working efficiency.
3. The extremely high stability of the fiber laser and the ultra-long life of the pump diode determine that it is not necessary to adjust the current to adapt to the aging problem of xenon lamp as the traditional lamp pump laser, which greatly improves the stability of production and product consistency.
4. The photoelectric conversion efficiency of the fiber laser is higher than 25%. The system has small power consumption, small size and small floor space.
5. Compact structure, high system integration, few faults, simple and easy to use, no optical adjustment, low maintenance or even zero maintenance, really achieving "light from the ground", plus anti-impact vibration, anti-dust, really suitable for industrial processing applications.
Leave a Comment