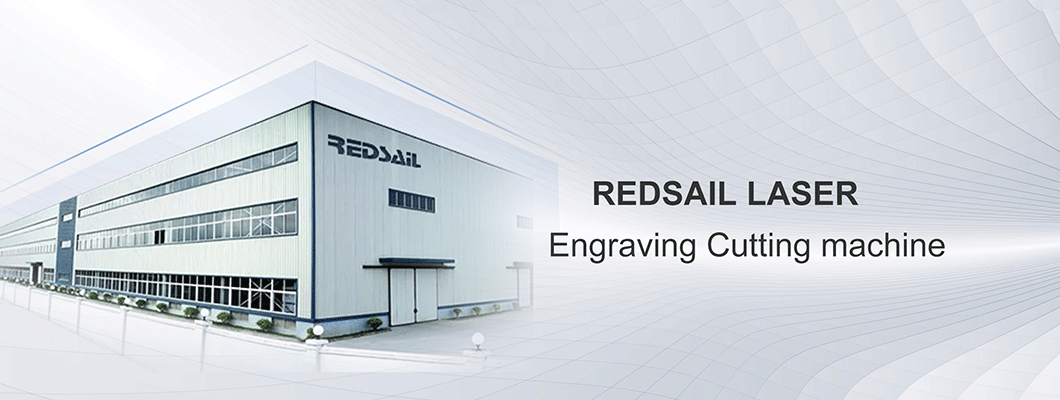
For laser cutting processing technology, some regular errors can be compensated by quantitative compensation method, but those random errors can only be eliminated by online detection or control. These errors mainly include:
1. Error caused by programming. In the process of 1D laser cutting, the machining path on the complex surface is fitted by straight lines, arcs, etc. There are some fitting curves and actual curves
These errors cause some errors in the relative position of the actual focus and the surface of the machining object and the ideal programming position. Some teaching programming systems also introduce some deviations.
2. Geometric error of the workpiece. The object of laser cutting is sheet metal or panel type parts. Due to the uneven surface of the processing object, the surface of these thin plates will be deformed due to the influence of thermal effect during laser cutting. For 1D laser processing, the surface of the panel will also be uneven during the pressing process, all of which will cause random changes in the position of the laser focus and the workpiece surface.
3. Error caused by workpiece clamping device. The workpieces processed by laser cutting are placed on the needle worktable. Due to processing errors, wear between the workpieces for a long time and laser barbecue, the needle bed will appear uneven, which will also produce random errors in the position between the thin steel plate and the laser focus.
Leave a Comment