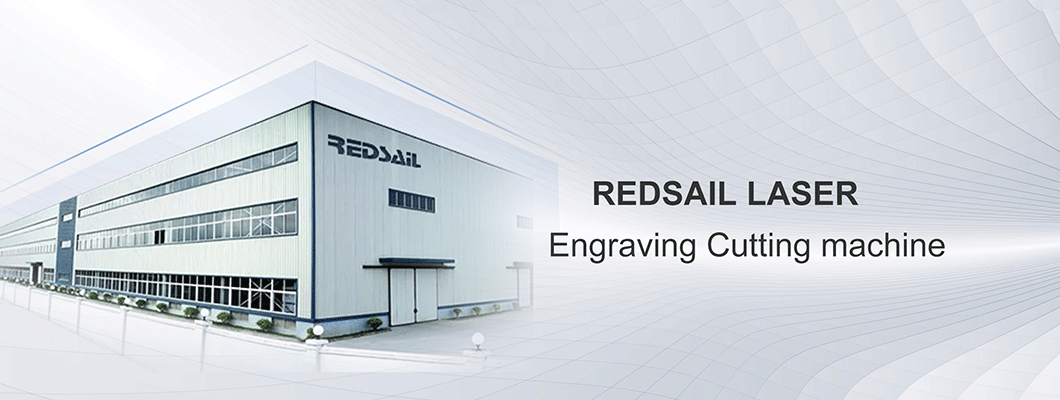
In the current metal processing industry, the more common steel is carbon steel, and optical fiber laser cutting machine has become one of the appropriate equipment for carbon steel cutting due to its high processing efficiency, high precision, no deformation and no burr after processing. To achieve an accurate cutting process, the cutting parameters need to be adjusted slowly. Here is a brief introduction of the influence of auxiliary gas on the cutting process during laser cutting.
There are three common auxiliary gases: air, nitrogen and oxygen.
1. Use air cutting
The advantages of using air cutting are obvious, and there is no cost. When using air, you only need to consider the electricity cost of the air compressor and equipment itself, saving the high auxiliary gas cost. The cutting efficiency on the thin plate is comparable to that of nitrogen cutting, which is an economical and efficient cutting method. However, air cutting also has obvious shortcomings on the section. First of all, the cutting surface will produce burrs, which requires secondary processing and cleaning, which is not conducive to the entire product production cycle. Secondly, the cutting surface will turn black, affecting the product quality. Laser processing itself has the advantages of efficiency and quality accuracy, while the shortcomings of air cutting cause many customers to give up this cutting method.
2. Cutting with oxygen
Oxygen cutting is a common and traditional cutting method. The advantage of optical fiber laser cutting machine using oxygen is mainly reflected in the cost of gas. In the sheet metal processing based on carbon steel, there is no need to change the auxiliary gas frequently, which improves the cutting efficiency and facilitates management. However, the disadvantage is that after oxygen cutting, there will be a layer of oxide film on the surface of the cutting surface. If the products with oxide film are directly welded, the oxide film will naturally peel off after a long time, and the welding will affect the welding quality.
3. Cutting with nitrogen
Use nitrogen for cutting. When oxygen is used as an auxiliary gas, an oxide film will form on the cutting surface. The use of nitrogen can prevent the appearance of oxide film and form non oxidative cutting. The surface of non oxidation cutting is generally white, which can be directly processed by welding, spraying and other methods. Its strong corrosion resistance also makes it widely used.
One of the functions of auxiliary gas is to blow away residual waste residue to achieve better cutting effect. The second is to use gas to chase away the metal slag while protecting the lens to prevent the slag from sticking to the lens and affecting the cutting quality.
For example, when cutting 1mm carbon steel with 4000W laser assisted by nitrogen, the speed can reach 35m/min, but there will be a little slag on the cutting surface. When using oxygen to cut 1mm carbon steel, the speed is only 10m/min, and the cutting surface is smooth without burrs. In fact, when cutting carbon steel within 3mm, air or nitrogen can be used for fast cutting, which is obviously faster than oxygen, but the disadvantage is that there is a little slag on the section.
Briefly describe the influence of auxiliary gas on laser cutting process
In this case, it is necessary to actually investigate the process that this batch of materials need to achieve. If the material has low requirements on the quality of the cut surface, air can be used for cutting. That is to save the cost of auxiliary gas, but also greatly improve the cutting speed. If the section accuracy is very high, oxygen must be used as the auxiliary gas.
Leave a Comment