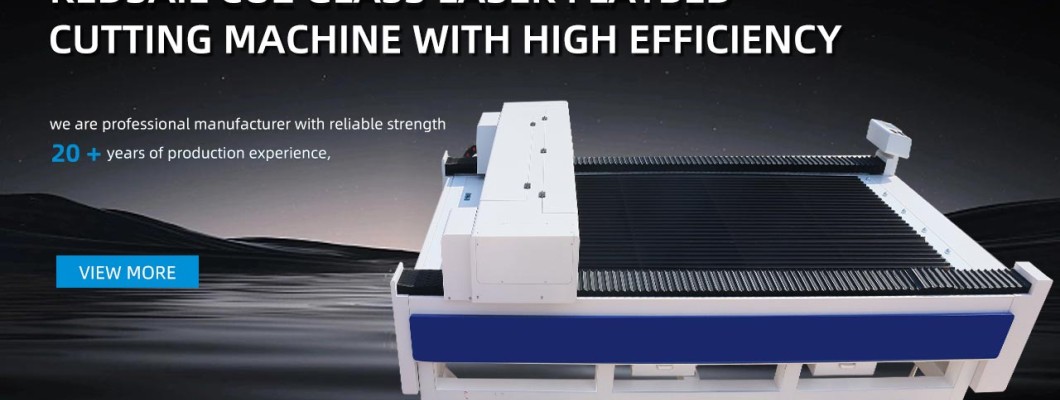
What are the factors that affect the cutting process and air pressure of a laser cutting machine?
The reason for the decrease in cutting speed under high auxiliary gas pressure can be attributed not only to the enhanced cooling effect of high airflow speed on the suspension zone, but also to the interference of intermittent shock waves in the airflow on the cooling of the laser zone. Uneven pressure and temperature can lead to changes in airflow density. This density gradient will change the refractive index within the field, thereby drying the focus of the beam energy, leading to refocusing or beam divergence. If the beam diverges too much, this interference can affect the melting efficiency and sometimes change the mode structure, leading to a decrease in cutting quality. Making the light spot too large can even cause serious consequences such as ineffective cutting.
1-211116104441410.png
2. The laser cutting machine uses compressed air as the auxiliary gas and requires air pressure.
The air contains water and oil, which can contaminate the laser lens after long-term use, making it difficult to achieve laser intensity and affecting the processing effect.
It doesn't matter if the thickness of the cut carbon steel plate is 3.5mm and the compressed air pressure is generally 1.0MPa. The flow rate depends on your demand for the cutting machine. Mainly related to stress. But if compressed air is used as an auxiliary gas.
There are still certain requirements for the quality of compressed air sources. Due to the contamination of the optical lens of the laser cutting machine by water, oil, and dust in compressed air, the optical path of the laser cutting machine deviates or sometimes does not penetrate during the cutting process.
Laser cutting machine during the cutting process
The beam is focused into a small focal point through the lens of the cutting head, achieving high power density, where the cutting head is fixed on the z-axis. At this point, the heat input by the beam far exceeds the heat reflected, transmitted, or diffused by the material, and the material quickly heats up to the melting and evaporation temperatures. At the same time, high-speed airflow blows out melted and evaporated materials from the coaxial or non coaxial sides, forming holes for material cutting. With the relative movement of the focus and material, the hole forms a continuous and narrow cutting seam, completing the cutting of the material.
3. What gases do laser cutting machines require for assistance?
Air is suitable for cutting aluminum plates and galvanized steel plates. To a certain extent, it can reduce the oxide film and save costs. Generally used for cutting plate thickness, with low requirements for cutting the end face.
2. Nitrogen.
Nitrogen is an inert gas that can prevent oxidation and combustion at the cutting end of the product (which can easily occur when the plate is thick). Nitrogen can be used for products that require high cutting ends without being exposed to the outside.
3. Oxygen.
It acts as a combustion aid and can improve cutting speed and thickness. Oxygen is suitable for thick plate cutting, high-speed cutting, and thin plate cutting, such as some large carbon steel and some thick carbon steel structural components. Oxygen can be used. Increasing gas pressure can increase the cutting speed, but after reaching the set value, continuing to increase gas pressure will reduce the cutting speed.
Leave a Comment