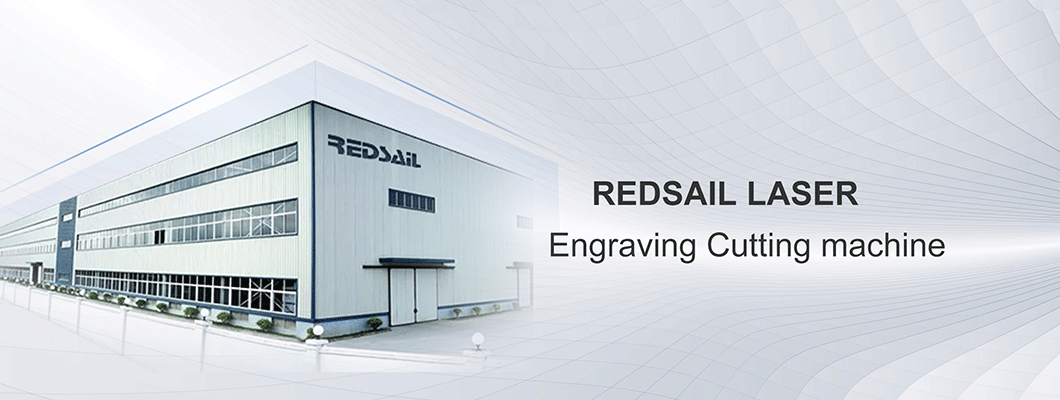
It is estimated that when using laser cutting machine to process sheet metal parts, many enterprises will feel that the cutting effect of laser cutting machine is not very good. For example, the most common is that there are many burrs on the cutting edge (burrs refer to various sharp corners, and rough edges and other irregular metal parts appear during the transition process of the workpiece surface during laser cutting), which will affect the appearance and accuracy of the product. If it is implemented twice, it will increase human and financial resources, which is very uneconomical.
With the rapid development of sheet metal processing industry, people have higher and higher requirements for product accuracy and appearance. Strictly speaking, products with burrs are unqualified products. How to prevent burrs when using laser cutting machine? The laser beam of the laser cutting machine is generally a pulse laser. When the metal plate is processed, the light output power per second is different, so the cutting surface will inevitably have fine bumps. Increasing the output frequency of the laser can reduce the roughness of the cross section.
When using the laser cutting machine, use high-purity auxiliary gas (the pressure of the auxiliary gas reaches 12-15kg) to assist the cutting, which can not only blow away the waste residue generated, reduce the occurrence of burrs, but also improve the surface finish.
Leave a Comment