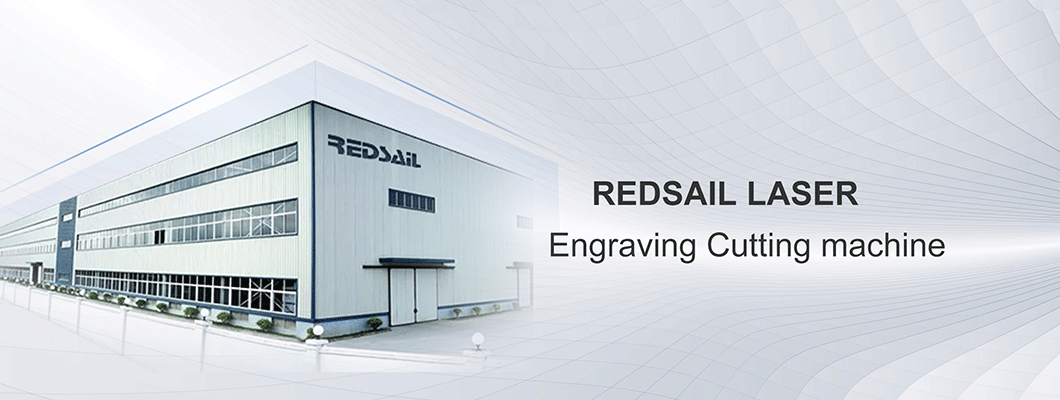
Many users of laser cutting machines are prone to hole bursting when cutting plates of more than 6mm, resulting in incomplete cutting samples or unstable follower. What causes it? Now, Ourui will list a few points for you to analyze.
【1】 Oxygen pressure
Oxygen is combustion supporting during laser cutting. When the drilling pressure is too high, the plate will break instantly, causing deflagration. Reduce the oxygen blowing pressure, and the perforation will slowly break through the plate without causing deflagration.
【2】 Air cutting
Laser cutting machine using air cutting will improve the hole bursting phenomenon, but the cutting speed will be reduced. Of course, you can also use inert gases such as nitrogen, but the gas cost will be higher.
【3】 Focus adjustment
It is complicated to adjust the focal length to solve the problem of hole bursting, so we need to debug step by step in the cutting sample to focus the focal length on the surface of the cutting plate. If the thick plate is cut, the cutting beauty will be reduced.
【4】 Upgrade device
Punching and cutting can effectively reduce the probability of hole bursting by adjusting the gas and air pressure of the laser cutting machine respectively.
Leave a Comment