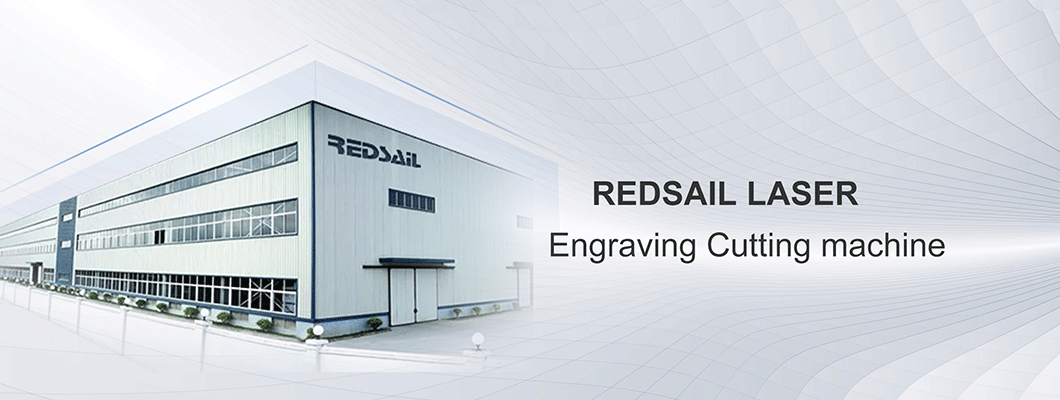
In the field of cutting processing, what we have to say is laser cutting and plasma cutting. Do you know the differences between them?
The principle of laser cutting processing is to use a high power density laser beam to scan the material surface, melt or vaporize the material in a very short time, and then use high-pressure gas to blow the melted or vaporized material away from the cutting seam, so as to achieve the purpose of cutting materials. Plasma cutting machine is a new type of thermal cutting equipment. Its working principle is to use the heat of high temperature plasma arc to locally melt the metal at the workpiece notch, and use the momentum of high-speed plasma to remove the molten metal to form a notch.
With the development of plasma cutting, the available working gas has a significant impact on the cutting characteristics, cutting quality and speed of plasma arc, but the cut is not as smooth as that of laser cutting, so there is generally no need for subsequent processing; In addition, the laser cutting has small heat affected zone, small plate deformation and narrow cutting seam (0.1mm~0.3mm); The notch is free of mechanical stress and shearing burr; High machining accuracy, good repeatability, and no damage to the material surface; Cutting NC programming, can process any plan, can cut the whole board with large format, without opening the mold, economical and time-saving.
Relative to the cutting accuracy, plasma cutting is rough machining, which can only reach within 1mm, while laser cutting can reach within 0.2mm; In terms of cost, plasma cutting is cheaper than laser cutting. In terms of processing accuracy, plasma cutting is more accurate than laser cutting! The selection of processing technology is also determined by the workpiece.
Leave a Comment