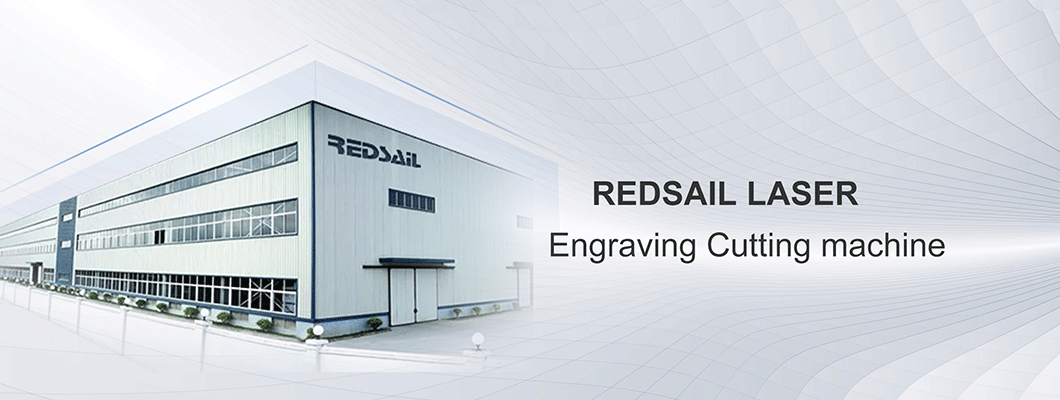
In the industry, laser cutting equipment has developed rapidly, with high processing power, which is conducive to the absorption of metal materials. So, what typesetting does laser cutting equipment have? Here's a detailed introduction.
1. Corner melting
When cutting the corner of the sheet steel at a reduced speed, the laser will melt the corner due to overheating. A small radius is generated at the corner to maintain high speed laser cutting and avoid overheating and melting of steel plates when cutting corners, so as to obtain good cutting quality, reduce cutting time and improve productivity.
2. Co cutting
Two or more types of parts share the same edge to form a combination. Large batches of regular graphics should share the same edge as much as possible. Cutting with the same edge can greatly shorten the cutting time and save raw materials.
3. Part spacing
In general, when cutting thick plates and hot plates, the distance between parts should be large, because the heat of thick plate hot plates has a great impact, and when cutting sharp corners and small figures, it is easy to burn edges, which affects the cutting quality.
4. Disposal of surplus materials
After the laser cutting equipment finishes cutting the parts, the skeleton like leftover materials on the workbench need to be removed as soon as possible to facilitate subsequent cutting operations. For the laser cutting equipment without automatic unloading device, the skeleton shaped residual material can be cut into small pieces to facilitate rapid removal. Thus, the operator's personal injury caused by moving heavy and sharp leftover materials is avoided.
5. Leader Settings
In the process of cutting thick plates, in order to ensure good connection of the cutting seams and prevent burns at the beginning and end of the cutting process, a section of transition line, called lead line and tail line, is often introduced at the beginning and end of the cutting process The lead wire and tail wire are useless to the workpiece itself, so they should be arranged outside the scope of the workpiece. At the same time, pay attention not to set the lead wire at sharp corners and other places that are not easy to dissipate heat. The connection between the lead wire and the kerf shall adopt arc transition as far as possible to make the machine move steadily and avoid burns caused by corner standstill.
Leave a Comment