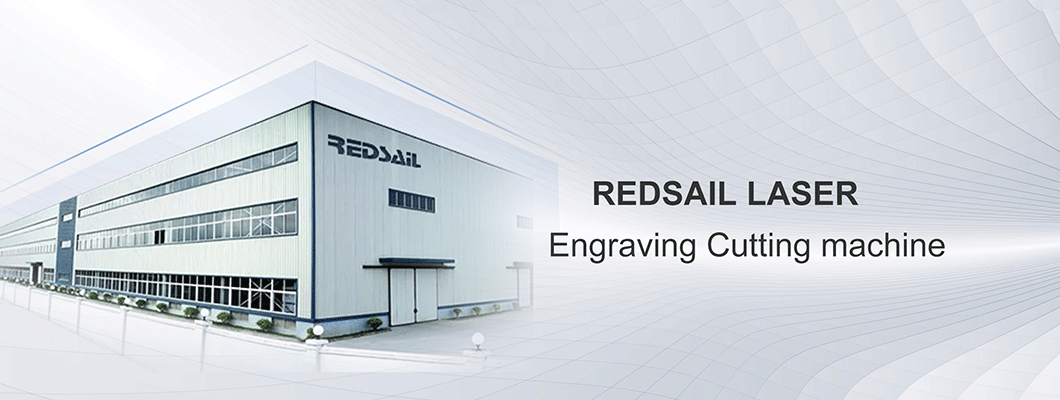
Introduction
Metal fabrication has revolutionized the manufacturing industry and now plays a crucial role in various sectors. Among the different techniques available, laser cutting has emerged as a leading technology due to its precision and versatility. This article explores the reasons why laser-cut metal is considered the best choice for achieving accuracy and versatility in various applications.
The Advantages of Laser Cut Metal
Laser cutting involves using a high-powered laser beam to precisely cut through various materials, including metals. This technique provides several advantages over traditional cutting methods, such as mechanical cutting or manual sawing. Here are the key reasons why laser-cut metal is preferred:
1. Precision
One of the main advantages of laser cutting is its exceptional precision. The laser beam can create intricate and precise cuts with a narrow kerf width, ensuring minimal material wastage. This precision allows for the creation of complex shapes and designs that would be challenging or impossible to achieve with other cutting methods.
2. Versatility
Laser cutting is compatible with a wide range of metals, including stainless steel, aluminum, brass, copper, and more. This versatility means that manufacturers can use laser cutting for various applications and industries, providing flexibility and adaptability in production. The ability to work with different metals opens up new possibilities in design and functionality.
3. Speed and Efficiency
Compared to traditional cutting methods, laser cutting is significantly faster and more efficient. The laser beam operates at high speeds, reducing production time and increasing overall efficiency. Additionally, laser cutting can be combined with computer-aided design (CAD) software, further streamlining the cutting process and enabling quick modifications to designs.
4. Clean Cuts and Smooth Edges
Laser cutting produces clean cuts with smooth edges, eliminating the need for additional machining or finishing processes. The laser beam's accuracy ensures that the edges of the cut material are clean and precise, minimizing the need for post-processing. This saves time, reduces costs, and improves overall productivity.
5. Reduced Risk of Material Distortion
Traditional cutting methods, such as mechanical cutting, can cause heat-affected zones (HAZ) and material distortion. In laser cutting, the laser beam's heat is focused and localized, minimizing the risk of HAZ. This is particularly crucial when working with delicate or thin materials that are sensitive to thermal deformation.
6. Design Freedom
Laser cutting allows for unparalleled design freedom. The ability to precisely cut complex shapes and intricate patterns enables designers and engineers to push the boundaries of creativity. Whether it's creating detailed decorative pieces or intricate parts for industrial machinery, laser-cut metal provides the freedom to transform ideas into reality.
7. Minimal Material Wastage
Laser cutting minimizes material wastage, making it an environmentally-friendly option. The laser beam's precision ensures that cuts are made with minimal excess material. This not only reduces waste but also results in cost savings by utilizing the maximum amount of material available.
FAQs
Q: Can laser cutting be used on all types of metals?
A: Laser cutting can be used on a wide variety of metals, including stainless steel, aluminum, brass, copper, and more. However, some metals, such as reflective metals, require specific laser types and settings to achieve optimal results.
Q: Is laser cutting a suitable method for industrial production?
A: Yes, laser cutting is widely used in industrial production due to its precision, speed, and versatility. It is commonly employed in industries such as automotive, aerospace, electronics, and manufacturing, among others.
Q: Does laser cutting cause any material damage?
A: Laser cutting minimizes material damage by focusing the heat on a localized area. However, it is important to consider the specific properties of the metal being cut, as some metals may be more susceptible to certain types of damage. Professional operators can help determine the appropriate laser settings to minimize material damage.
Q: Can laser cutting be used for both thick and thin metals?
A: Yes, laser cutting is suitable for both thick and thin metals. With adjustments in laser power and speed, operators can achieve clean cuts with minimal heat distortion on a wide range of metal thicknesses.
Q: How can I benefit from laser-cut metal in my design projects?
A: Laser-cut metal provides design freedom and precision, allowing you to create intricate and unique designs. It also ensures clean and smooth edges while minimizing material wastage. By leveraging the advantages of laser cutting, you can bring your design ideas to life with precision and efficiency.
Conclusion
Laser cut metal offers unparalleled precision and versatility, making it the best choice for various applications. Whether in industrial production, customization, or creative projects, laser cutting ensures clean cuts, smooth edges, and design freedom. Its time-efficiency, minimal material wastage, and compatibility with multiple metals further contribute to its preference over traditional cutting methods. With the continuous advancement of laser technology, the future looks promising for this versatile metal cutting technique.
Leave a Comment