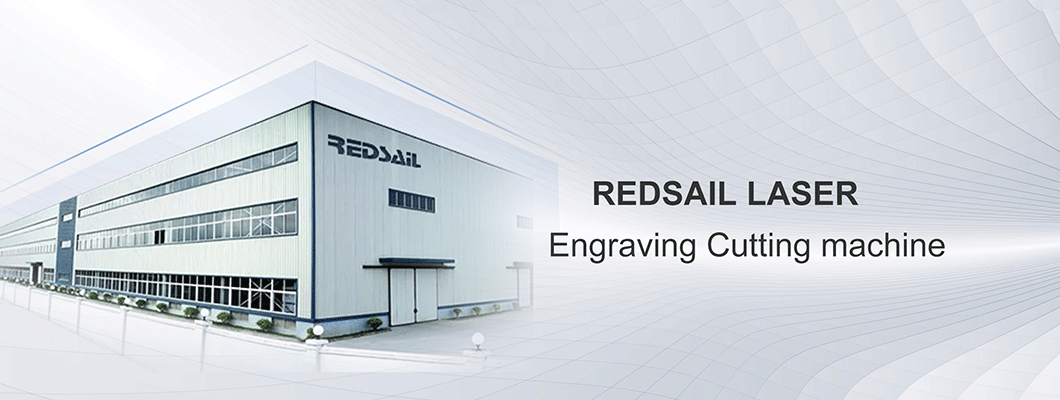
Laser pipe cutting machine is the main equipment for pipe cutting in use. Whether it is square pipe, round pipe or special-shaped pipe, it can be effectively cut. It has more advantages than other equipment in pipe cutting. With its professional and stable cutting effect, the pipeline laser cutting machine quickly occupied various metal processing industries, especially in the automobile manufacturing industry and oil development field. Mining and machinery manufacturing have been widely used.
The laser processing of laser pipe cutting machine is completed by computer drawing and plate making. The operation is simple and convenient. In terms of graphics processing, it can flexibly process any graphics. Moreover, it can realize large-scale, fast and accurate processing. The cutting process can complete multi-step processing at one time, and the cutting speed of a few meters long pipe in one minute is higher than that of other cutting methods.
Working principle and operating advantages of laser cutting machine
Working principle of laser pipe cutting machine:
1. Loading rack: Before cutting, it is necessary to manually lift the whole bundle of pipes to the placement rack, then manually pack and remove them, and then place them on the automatic pipe conveying mechanism in turn.
2. Place the pipes on the conveying platform in turn. The pipe conveying device can transfer one pipe to the feeding mechanism at a time as required, and automatically supply for standby according to the pipes.
3. The feeding mechanism will automatically transfer the pipes in the waiting area to the automatic feeding mechanism according to the signal, and other pipes will automatically fill and move to the material position to ensure continuous operation.
4. The pipe positioning and calibration system shall calibrate the position of the pipe as required (the pipe material shall not be placed outside the feeding mechanism).
5. The feeding structure will automatically send pipes to the machine tool material (lifting) shelf system (one pipe at a time) according to the signal.
6. After receiving the shelving signal, the paper feeder returns in time. At the same time, the rotary gripper moves according to the signal, clamps and pushes forward to the rotary table B to achieve perfect cutting.
7. The material rack system automatically lifts according to the distance of the rotary claw device to avoid collision;
8. When the rotary claw device moves forward to the middle limit position of the B rotary support plate, the C rotary claw device automatically runs to the right end of the B rotary table to continue to perfectly cut the tailings, so as to ensure the overall cutting of pipe materials, and the tailings are basically zero.
9. The rotation distance between the automatic lifting material receiving system and the pipe shall be increased by 15mm. When cutting off the pipe, the workpiece shall be grasped to avoid excessive clearance at the cutting point or falling deformation due to self weight. The pipe when the workpiece falls naturally.
10. After the completion of the automatic lifting material receiving system, it will automatically drop to a fixed position, at the same time, the receiving box will tilt, and the workpiece will naturally slide to the ground material collecting bucket.
11. Before cutting the previous tube, the feed mechanism is ready and the next tube is ready for processing.
Leave a Comment