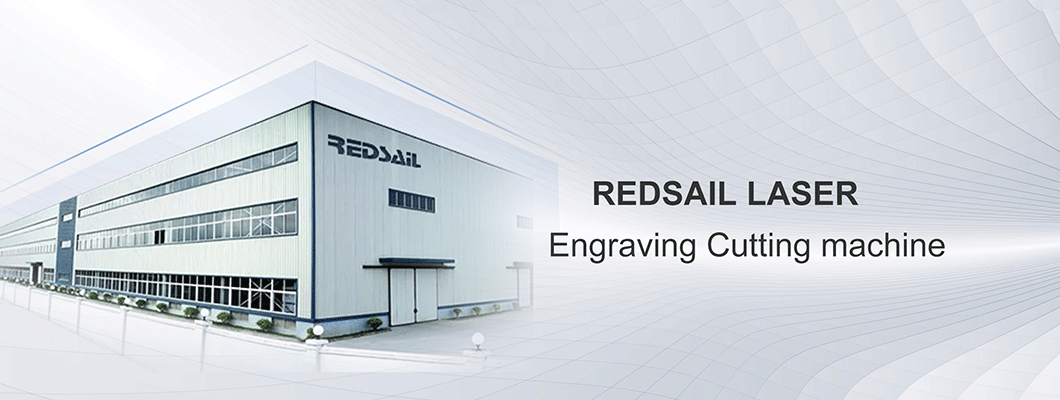
With the rapid development of China's economy, the quality of life of the people has gradually improved. The automobile is no longer a simple means of transportation. People are more interested in the good dynamic performance and design aesthetics of the automobile. At present, the automobile has been popularized in every household in China, and the production and manufacturing of automobiles in large quantities and in various forms has become normal. With the need of the automobile manufacturing industry to meet the continuous upgrading of export and domestic manufacturing, the traditional automobile processing technology and body parts can no longer meet the current product quality and production needs. The birth of laser cutting machine has played a key role in the production and manufacturing of automobile sheet metal
Traditional metal processing methods mainly include plate cutting, punch, flame cutting, water cutting, etc. After the preliminary processing materials are formed, the frontal angles and burrs generated during processing need to be polished again. Inadequate processing technology leads to low production efficiency, difficult to achieve processing accuracy, and can not meet the processing requirements of sheet metal parts with complex shape and high accuracy requirements in automobiles. From the perspective of technology and economy, if you want to improve the safety performance of cars, you must ensure the cutting accuracy of assembly materials.
As an advanced means of metal processing, laser cutting has taken the lead in many developed industrial countries and played an important role in the field of automobile manufacturing. Auto parts, car doors, car bodies, car door frames, car boot and car roof, car wheels, and many precision parts can be processed by laser cutting machines.
The laser cutting machine has become the preferred processing equipment in the automobile sheet metal manufacturing industry because of its high cutting accuracy, fast production speed, burr free cutting, adaptability to the processing of various complex features accessories, one-time molding and other characteristics. The advantages of laser cutting equipment are very prominent, which can be summarized in the following aspects during processing:
1、 High precision smooth cutting
The laser cutting equipment adopts intelligent operation control system and professional laser cutting software, with high cutting accuracy, fast production speed and smooth cutting. It can accurately cut complex patterns, with minimal error and ease of production!
2、 Save production costs
The production cost of laser cutting equipment is 50% of that of traditional cutting. The use of laser cutting machine can replace the blanking and production of traditional processing molds, saving a lot of mold manufacturing costs. Cutting "zero tailings" can achieve high utilization rate of plates and reduce production costs of users.
3、 High machining flexibility
The laser cutting machine can be used for flexible processing, the intelligent cutting software can edit various complex graphics, and the small batch, large area and complex contour plates can also be cut freely! The laser cutting equipment has a large processing area, which can process the whole plate, meet the personalized production needs of users, and realize flexible processing.
4、 Suitable for accessories made of various materials
The laser cutting machine supports cutting various metal plates and pipes, and is mainly used for cutting stainless steel, carbon steel, aluminum, brass and alloy metal materials. The cutting surface is flat and smooth, with strong adaptability.
Leave a Comment